BYD’s Motor Core Mould Components: Unleashing Efficiency in Global EV Markets
In the global new energy vehicle market, BYD stands out with its excellent technology and large market share. Its success not only stems from its own R & D strength but also from the close cooperation with suppliers to jointly overcome cost and efficiency challenges. Motor core mold parts, as a crucial component of the new energy vehicle drive system, play a vital role in this process.
Cost Reduction of BYD and Supplier Collaboration
In recent years, BYD has demonstrated strong cost – control capabilities in the new energy vehicle market. In 2024, with a remarkable sales volume of 3.02 million units, BYD effectively reduced the production cost per vehicle through economies of scale. Meanwhile, the price of key raw materials such as lithium carbonate dropped significantly from four to five hundred thousand yuan per ton to less than one hundred thousand yuan, providing broad space for BYD’s cost optimization.
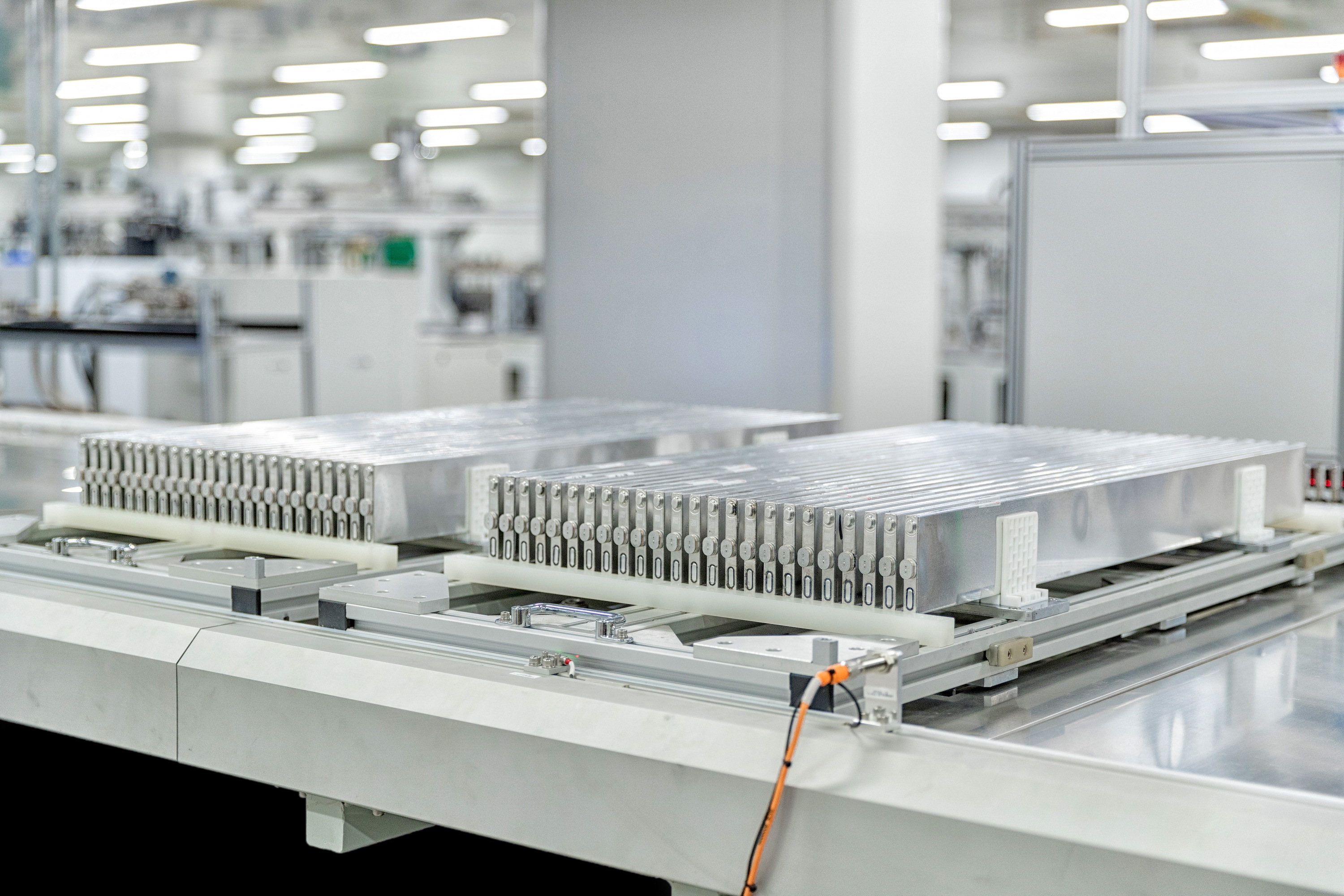
Suppliers play a key role in this process. For example, in the face of BYD’s strict requirements for production materials, NeoAlu, with its leading industry experience and technical advantages, actively invested in research and development. Through material research and development and optimized design, it developed a stronger and lighter battery – box material. This not only meets BYD’s requirements for material strength and stability but also significantly reduces the raw – material cost of the battery box. This cooperation not only helps BYD achieve cost reduction but also promotes technological progress in the electric – vehicle industry.
Another example is LinTai New Materials. As a supplier of friction plates for BYD’s automatic transmissions, through domestic substitution, it reduced the cost of BYD’s procurement of automatic – transmission components. This enables BYD to invest more resources in the research and development and promotion of intelligent – driving technology, enhancing the overall competitiveness of its products.
The Crucial Impact of High – Efficiency Stamping Dies on the Production Efficiency of New Energy Vehicles
In the production of new energy vehicles, the efficiency of molds is directly related to production capacity and cost. Traditional molds have many pain points during the production process, such as long molding cycles and low energy efficiency, resulting in low production efficiency and restricting the promotion of new energy vehicles. For example, when producing throttle valves for new energy vehicles, traditional die – casting molds often face problems such as thermal expansion and thermal fatigue caused by high temperatures and frequent thermal cycles, which affect product quality and production efficiency.
High – efficiency stamping dies can effectively solve these problems. Take the integrated die – casting mold patent for throttle valves of new energy vehicles applied by Ningbo Saiweida Technology Co., Ltd. as an example. This technology improves the stability and durability of the mold through an integrated die – casting mold and uses a dynamic heat – regulating component and high – thermal – conductivity insertion columns to regulate the mold temperature in real – time. This significantly shortens the molding cycle, ensures the molding quality and service life of die – castings. This not only improves the product – qualification rate but also speeds up the automobile production process, enabling enterprises to launch more competitive new models faster.
Actual production data shows that after adopting high – efficiency stamping dies, the production cycle can be shortened by 30% – 50%, and the product – qualification rate can be increased by 10% – 20%, effectively improving the production efficiency of new energy vehicles.
Analysis of Efficiency Improvement through Optimization of Motor Core Stamping Die Parts
The key parts of motor – core stamping dies, such as roller guide post sets, have a significant impact on the performance and production efficiency of the molds. Different from ball guide post sets, the contact area of rollers in roller guide post sets is about 10 times larger than that of balls. Using rollers can improve the rigidity between the guide post and the guide sleeve.
In terms of material upgrading, manufacturing roller guide post sets with new high – strength and wear – resistant materials can effectively reduce wear and improve stamping accuracy. For example, we have developed a new material for roller guide post sets, and its wear resistance is 50% higher than that of traditional materials. This makes the positioning of the mold more accurate during the stamping process, and the stamping accuracy is increased by 20%, thereby improving the manufacturing quality of the motor core.
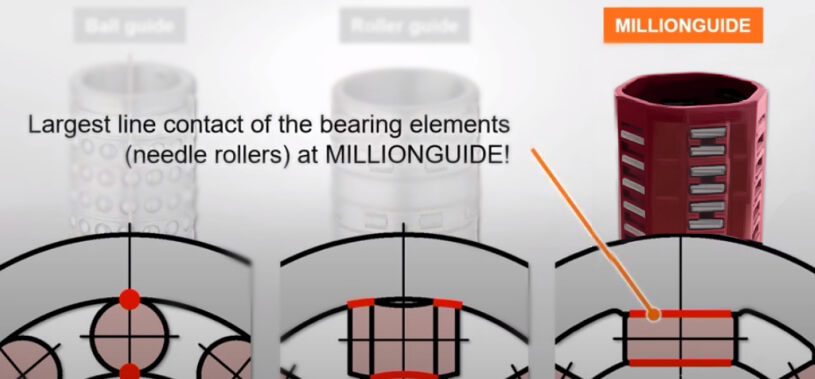
In terms of structural optimization, improving the structural design of roller guide post sets enables them to better adapt to high – speed stamping conditions and reduce maintenance time. For example, the optimized structure of roller guide post sets reduces the friction coefficient while ensuring strength, making the mold more stable during continuous stamping. The maintenance cycle has been extended from once a month to once a quarter, greatly improving production efficiency.
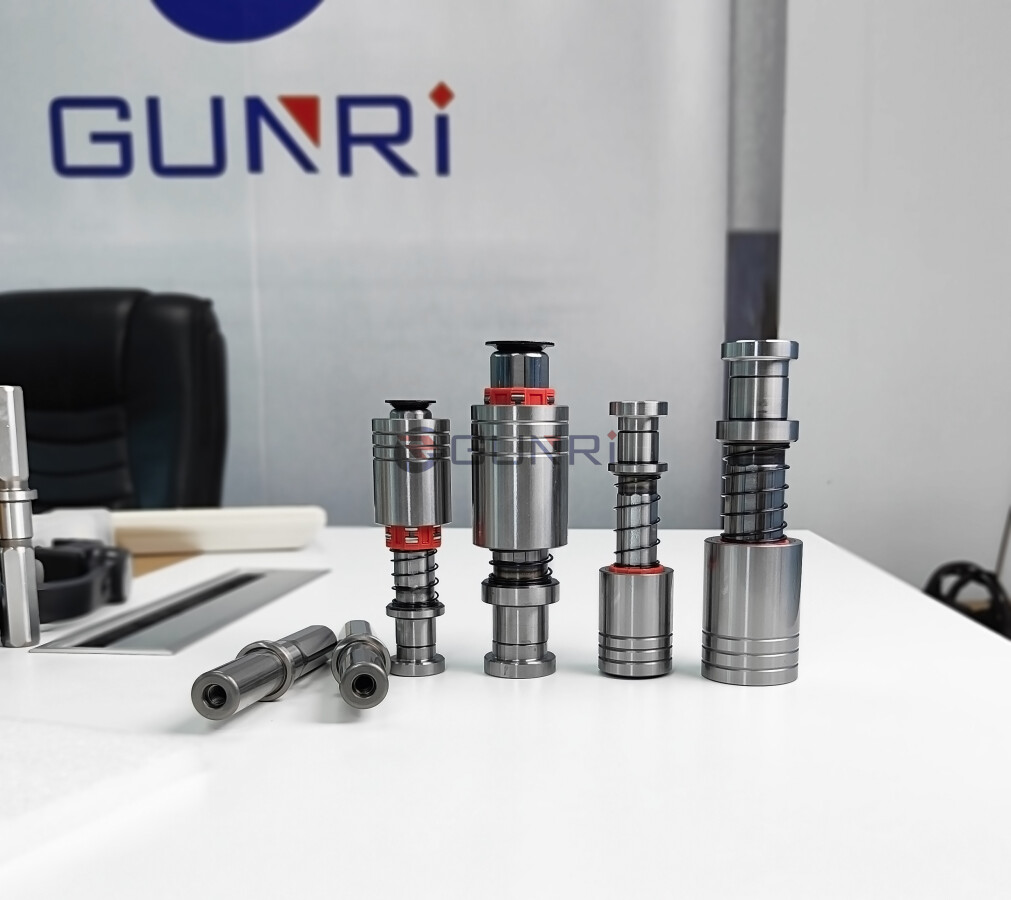
Through a chart comparison, it can be clearly seen that before the improvement, the production efficiency of the motor – core stamping die was 500 pieces per hour, and the defective rate was 8%. After the improvement, the production efficiency increased to 800 pieces per hour, and the defective rate decreased to 3%, and the production efficiency has been significantly improved.
Conclusion and Inquiry Guidance
The optimization of motor – core stamping die parts is crucial for improving the production efficiency and product quality of BYD new energy vehicles. From material innovation to structural optimization, every improvement in each link provides strong support for the efficient drive of new energy vehicles.
As one of the few enterprises that can provide a full range of customized roller guide post sets, our company has rich industry experience and advanced production technology. We have provided customized roller guide post set solutions for many well – known automotive manufacturing enterprises, helping customers improve production efficiency and reduce production costs. For example, for a new energy vehicle enterprise, the high – performance roller guide post sets we provided extended the service life of its molds by 50% and increased the production efficiency by 30%.
If you have any needs for motor – core stamping die parts of new energy vehicles, please feel free to contact us. We will wholeheartedly serve you and work together to create a better future for the new – energy – vehicle industry.