Customizable Nitrogen Gas Springs
Introduction to Nitrogen Gas Springs
Nitrogen gas springs are essential components in various industrial applications due to their superior performance, reliability, and customization options. These springs are widely used in die-casting, automotive, and manufacturing industries where precise and powerful force is required. At GUNRI, we pride ourselves on delivering high-quality, customizable nitrogen gas springs that cater to the unique needs of our clients.
The Science Behind Nitrogen Gas Springs
Nitrogen gas springs operate on the principle of compressed nitrogen gas. Unlike traditional mechanical springs, nitrogen gas springs offer consistent force and longer service life. The gas spring consists of a cylinder filled with high-pressure nitrogen gas and a piston rod that moves within the cylinder. As the piston rod compresses, the nitrogen gas is compressed, creating a powerful and consistent force.
Advantages of Customizable Nitrogen Gas Springs
Enhanced Performance and Durability
One of the primary advantages of nitrogen gas springs is their enhanced performance and durability. These springs are designed to withstand high cycles and extreme conditions, making them ideal for demanding industrial applications. The use of high-quality materials and precise manufacturing techniques ensures that our nitrogen gas springs offer superior performance and longevity.
Precision and Consistency
Nitrogen gas springs provide precise and consistent force, which is crucial for applications that require accurate and reliable performance. The ability to customize the force and stroke length of the springs allows for tailored solutions that meet the specific requirements of each application. This precision and consistency lead to improved productivity and reduced downtime.
Customization Options
We offer a wide range of customization options for nitrogen gas springs. Clients can specify the force, stroke length, cylinder diameter, and other parameters to ensure that the springs meet their exact needs. Our team of experts works closely with clients to understand their requirements and develop customized solutions that enhance their operations.
Applications of Nitrogen Gas Springs
Automotive Industry
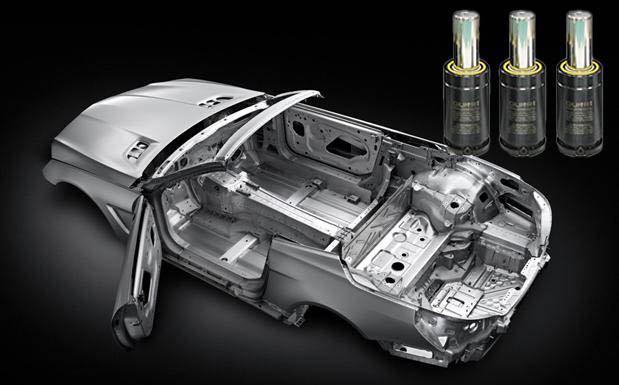
In the automotive industry, nitrogen gas springs are used in various applications, including stamping, forming, and molding. These springs provide the necessary force and precision required for manufacturing high-quality automotive components. The ability to customize the springs ensures that they can be tailored to meet the specific needs of different automotive applications.
At an automotive stamping plant, the introduction of customized nitrogen gas springs resulted in a 15% increase in production efficiency. The plant needed springs with specific force and stroke length to optimize their stamping process. By implementing our customized nitrogen gas springs, the plant reduced downtime and improved the quality of stamped parts, leading to significant cost savings.
Die-Casting and Molding
Nitrogen gas springs are essential in die-casting and molding applications, where precise and powerful force is required. These springs help improve the efficiency and quality of the casting and molding processes. Customizable nitrogen gas springs ensure that the force and stroke length are optimized for each specific application, leading to better results and reduced waste.
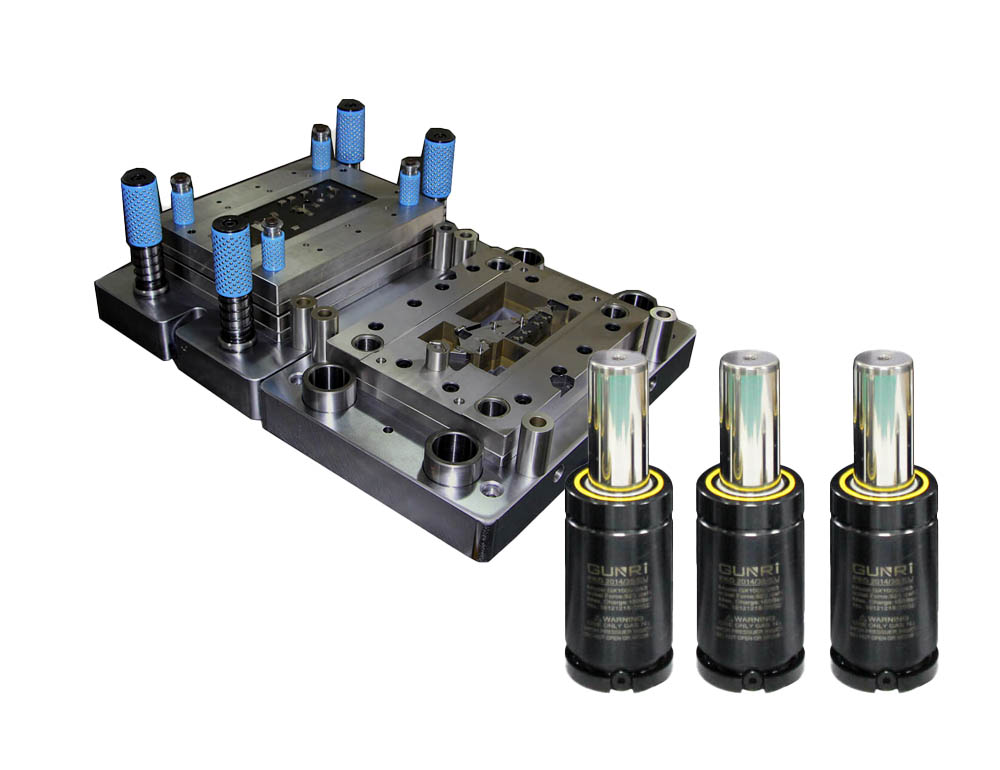
A molding company faced challenges with inconsistent force application, resulting in defective products. By switching to our customizable nitrogen gas springs, they achieved a 20% reduction in defective parts. The ability to fine-tune the springs to their specific molding requirements allowed for consistent and reliable force application, enhancing product quality.
Manufacturing and Industrial Applications
In manufacturing and industrial applications, nitrogen gas springs are used in various machines and equipment to provide consistent and reliable force. These springs help improve the efficiency and performance of machines, leading to increased productivity and reduced maintenance costs. The ability to customize the springs ensures that they are perfectly suited for each application, enhancing overall performance.
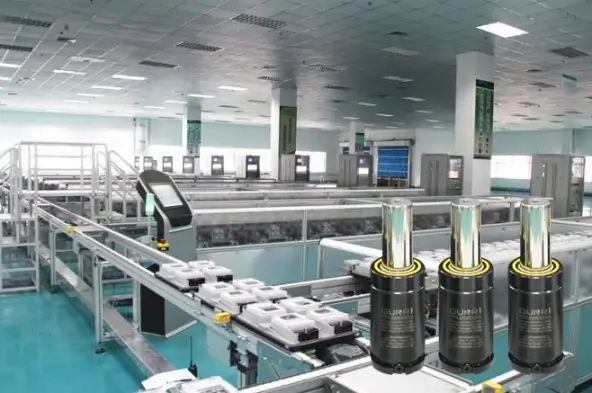
An industrial equipment manufacturer required nitrogen gas springs with precise specifications to enhance their machine’s performance. After implementing our customized springs, the manufacturer reported a 25% increase in machine efficiency and a 30% reduction in maintenance costs. The tailored springs provided consistent force, reducing wear and tear on the equipment.
Customization Process
Understanding Client Requirements
The first step in the customization process is understanding the specific requirements of our clients. Our team of experts works closely with clients to gather detailed information about their applications and performance needs. This information is used to develop a comprehensive understanding of the client’s requirements and to identify the best solutions.
Design and Development
Once the requirements are understood, our team of engineers and designers works on developing customized nitrogen gas springs. Using advanced design software and state-of-the-art manufacturing techniques, we create springs that meet the precise specifications of our clients. The design process involves selecting the appropriate materials, determining the optimal force and stroke length, and ensuring that the springs meet all necessary standards and regulations.
Testing and Quality Assurance
Before delivery, all customized nitrogen gas springs undergo rigorous testing and quality assurance processes. This ensures that the springs meet the highest standards of performance and reliability. We use advanced testing equipment and techniques to verify the force, stroke length, and overall performance of the springs. Our commitment to quality ensures that our clients receive springs that deliver superior performance and durability.
Delivery and Support
After the springs have been tested and approved, they are delivered to our clients. We offer comprehensive support to ensure that the springs are installed and functioning correctly. Our team is available to provide assistance and address any issues that may arise. We also offer ongoing maintenance and support services to ensure that the springs continue to perform at their best.
Choosing the Right Nitrogen Gas Springs
Factors to Consider
When selecting nitrogen gas springs, several factors need to be considered to ensure the best performance and reliability. These factors include the force required, stroke length, cylinder diameter, and the specific application requirements. Our team of experts can help clients navigate these factors and select the best springs for their needs.
Benefits of Customization
Customizable nitrogen gas springs offer several benefits over standard springs. By tailoring the springs to meet specific requirements, clients can achieve better performance, increased efficiency, and longer service life. Customization ensures that the springs are perfectly suited for their intended applications, leading to improved results and reduced costs.
Contact Us for Your Customizable Nitrogen Gas Springs
At GUNRI, we are committed to providing customizable nitrogen gas springs that meet your specific needs and exceed your expectations. Our extensive experience and dedication to quality ensure that we deliver products that enhance performance and reliability in any application.
For more information about our customizable nitrogen gas springs and to discuss your specific requirements, please contact us. Our team of experts is ready to assist you with tailored solutions that will help optimize your operations and achieve superior results. Don’t hesitate to reach out to us and experience the exceptional quality and performance of GUNRI’s nitrogen gas springs.