Design Considerations for Efficient Torsionally Flexible Couplings
Regardless of the application, couplings must meet various requirements to ensure the efficient and reliable operation of the coupling system. Undoubtedly, couplings are a crucial component of the entire propulsion system. Therefore, when designing couplings, attention must be paid to their ability to withstand mechanical demands, require minimal maintenance, operate without failures, and ideally have a long service life.
Torsionally Flexible Couplings
Torsionally flexible couplings, which are non-displaceable, are primarily used for torque transmission. In addition to reliable torque transmission, the ability to compensate for shaft misalignment is another key factor in selecting couplings, and shaft misalignment typically occurs only during on-site operations. There are distinctions between angular, radial, and axial shaft misalignments, and these misalignments must be controlled within predetermined ranges.
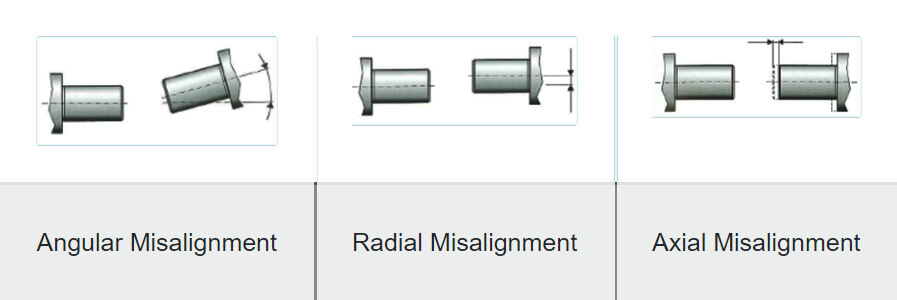
Most importantly, by appropriately selecting the elastomeric coupling elements, the natural frequency of the drivetrain can be shifted to non-critical speed ranges, allowing the torsionally flexible coupling to provide compensation for torsional vibration amplitudes and shock torques. Therefore, stiffness and damping characteristics are also crucial parameters when designing torsionally flexible couplings.
Design Standards in Focus
The layout design of torsionally flexible couplings must consider size-related attributes. These include the maximum driving torque, maximum speed, and the required torsional stiffness and damping behavior depending on the circumstances. However, equipment-related parameters, such as environmental temperature and potential misalignments of connecting shafts, are also of great importance.
Torque Calculation
The permissible torque of the coupling is of significant importance for optimizing the design. The allowable torque is the maximum torque that may occur during the operational process. Additionally, the coupling must be able to withstand specific transient loads, such as during start-up and shutdown, electrical or mechanical conversions, and braking or acceleration operations.
Stiffness Considerations
Stiffness is the ability of an object or material to resist elastic deformation caused by external forces (such as torque or force). For torsionally flexible couplings, torsional stiffness is a crucial parameter. Stiffness depends on the material’s elasticity and the shape and size of the main cross-sectional area. The elastic performance of torsionally flexible couplings largely depends on the elastomeric buffers arranged within the coupling.
Challenges of Vibration
If the system is periodically excited at a frequency corresponding to the system’s natural frequency, the vibration amplitude will steadily increase, known as “resonant swing-up.” If vibration is not damped, the amplitude will continue to increase until the system is damaged – a phenomenon known as resonance catastrophe.
Damping is primarily determined by the selected elastomeric material, and the vibration amplitude will present limited values. Such vibrations can be generated, for example, by reciprocating piston-type diesel engines. The torque transmitted to the drive device by the combined action of the cylinders is often subject to severe fluctuations. These vibrations must be appropriately attenuated during operation.
Temperature and Climate as Focus
Another decisive parameter is temperature. Both ambient temperature and operating temperature directly affect the elastomeric material’s power transmission capability. Higher ambient temperatures strongly impact mechanical stability. These factors must be considered in the early design stages by taking into account application-specific factors to avoid potential damage, premature failure, and breakdowns. If high-performance polyurethane is used as the elastomeric buffer in torsionally flexible couplings, humidity also plays a significant role.
For example, if elastomeric couplings are used in the drive systems of sugar mills operating in tropical climates, special measures need to be taken. In some cases, corrosion resistance is a requirement that must be considered, necessitating the selection of high-quality materials for coupling components. Alternatively, suitable surface protection methods, such as nickel plating or electroplating, can be chosen.