Distinguishing Surface Roughness and Surface Finish
Table of contents
What is Surface Roughness?
Surface roughness, also known as roughness, is a critical aspect of surface finish commonly specified, measured, and calculated. It is defined by variations in the direction of actual surface normal vectors compared to their ideal form. Significant variations classify a surface as rough, while minimal variations deem it smooth.
In surface metrology, roughness is often associated with high-frequency and short-wavelength components of the measured surface. However, practical applications require considering both amplitude (size of deviations) and frequency (frequency of deviations) to determine surface suitability.
What is Surface Finish?
Surface finish refers to surface texture and is often used interchangeably with “surface texture.” It consists of three main components: roughness, flatness, and waviness. The surface finish of finished products may vary significantly depending on materials and manufacturing processes.
Specifications for surface finish are typically indicated on technical drawings of mechanical parts, especially when parts need to fit closely, interact, or form seals. To correctly specify and interpret surface finish symbols on technical drawings, the American Society of Mechanical Engineers (ASME) has published the Y14.36M Surface Texture Symbols standard. ASME also released the B41.6 Surface Texture standard, providing definitions and measurement methods.
Effectively communicating surface requirements is crucial for ensuring the final product meets performance standards. Failure to include, accurately specify, or correctly interpret surface finish requirements can significantly impact the final product’s performance and cost.
Different Surface Treatments
In general, products requiring high purity demand manufacturing equipment with a finer surface finish. For instance, 2B surface treatment is commonly used in baking, food processing, pharmaceuticals, vacuum drum dryers, and containers. This treatment is considered smooth, sometimes even smoother than polished #4 surface treatment, both meeting USDA standards. The average roughness (Ra value) for 2B surface treatment typically ranges between 0.3 (12) and 1μ (40), depending on metal specifications.
Other finishes and their corresponding average roughness values for comparison include:
- #1 surface treatment (HRAP): Initial state, very rough surface (Ra 3.2-12.5).
- #4 finish: Straight-line finish, standard Ra around 0.8, with dairy or sanitary surface treatment falling between 0.3 and 0.4 Ra.
- #7 and #8 finishes: Polished finishes, #8 being nearly flawless with an Ra value of 0.025.
For biopharmaceutical applications, a surface finish of approximately 0.38 Ra achieved through electropolishing is typically specified, complying with the BPE SF-4 standard. Powder and tablet manufacturers may use a slightly rougher surface finish of around 0.5 Ra according to the BPE SF-2 standard, as it does not require electropolishing.
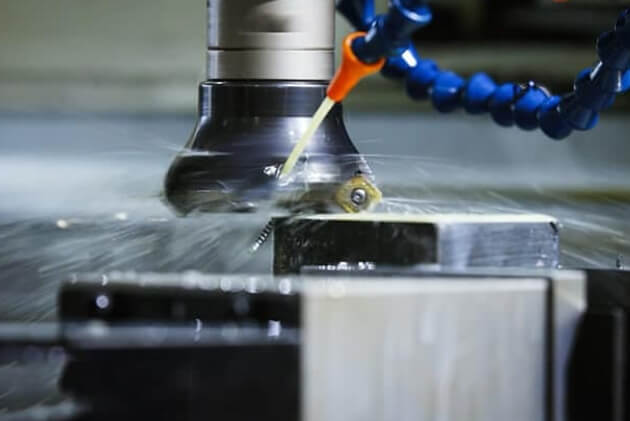
Distinguishing Surface Roughness and Surface Finish
Surface finish encompasses three key elements: roughness, flatness, and waviness, with roughness being the most commonly specified aspect.
Roughness refers to the measurement of macroscopic and microscopic irregularities on the processed surface of a finished product. It provides a quantitative indication of peak heights and valley depths of these surface irregularities. Various instruments can be used for precise roughness measurements.
Conversely, surface finish qualitatively describes and specifies the overall appearance and quality of a surface. This can be achieved through visual observation of the surface or by considering roughness values. Descriptive attributes such as poor, fair, good, glossy, fine, etc., are used to characterize finish quality. Unlike roughness, surface finish does not yield numerical values and may be subject to subjective human perception.
The table below summarizes the main distinctions between surface roughness and surface finish.
Surface Roughness | Surface Finish |
---|---|
Quantitative measurement of surface irregularities | Qualitative evaluation of surface quality |
Provides numerical values for peak heights and valley depths | Described using attributes such as poor, fair, good, glossy, fine, etc. |
Measured using specific instruments | Evaluated visually or determined based on roughness values |
Objective measurement | Subjective assessment |
Aids in assessing functional aspects such as friction and wear | Represents the overall appearance and aesthetic appeal of the surface |
Has both quantitative and qualitative value
All physical parameters are measurable, and their values are expressed in numerical terms along with corresponding units. Quantitative measurements always provide numerical values and units. Surface roughness is an example of a measurable parameter; for instance, the average roughness of a micro-ground surface may be 325 nanometers. On the other hand, smoothness is a qualitative parameter and cannot be expressed numerically. Instead, attributes like good, poor, fair, rough, etc., are used to describe the finish.
Subjective parameters and human perception
Surface finish attributes are subjective and depend on specific applications or desired outcomes. For example, a milling surface considered to have good finish for a casing may be viewed as having a poorer finish if intended for use in ball bearings. However, roughness remains constant regardless of the application. It is independent of the application and is not influenced by human biases. Due to differing human preferences, what one person considers a good finish, another may not. Therefore, attributes used to describe surface finish have limited applicability in a scientific context.
Measuring instruments
Various easily obtainable contact and non-contact instruments can be used to accurately measure surface roughness. These instruments have different characteristics and functionalities. Regardless of the specific measuring instrument used, roughness is essentially a measurement of peak heights and valley depths on the object’s surface. Conversely, surface finish cannot be directly measured using instruments. Instead, roughness values are used as an indirect indicator to specify surface finish.
Using other parameters for assessment
Different manufacturing processes result in varying degrees of surface finish. Typically, processes involving surface generation, such as mechanical machining, and surface modification technologies like heat treatment, coating, and coloring, often lead to reduced roughness. However, newer and more advanced processes like powder metallurgy and investment casting can also provide high-quality surfaces. Estimating roughness can be done by considering various process parameters and relevant instrument functionalities used in the process. For example, when machining with sharp tools, estimated roughness can be expressed using parameters such as feed rate, primary cutting edge angle, and secondary cutting edge angle. However, surface finish cannot be estimated in the same way.