English Article: Eccentric Shaft in RV Reducers – Applications and Procurement Considerations
The Eccentric Shaft (also known as the Crankshaft in some technical contexts) is a critical component in RV Reducers (Rotation Vector Reducers), which are widely used in robotics, precision machinery, and industrial automation. This article explains where and how the eccentric shaft functions within an RV reducer and highlights key considerations for procurement.
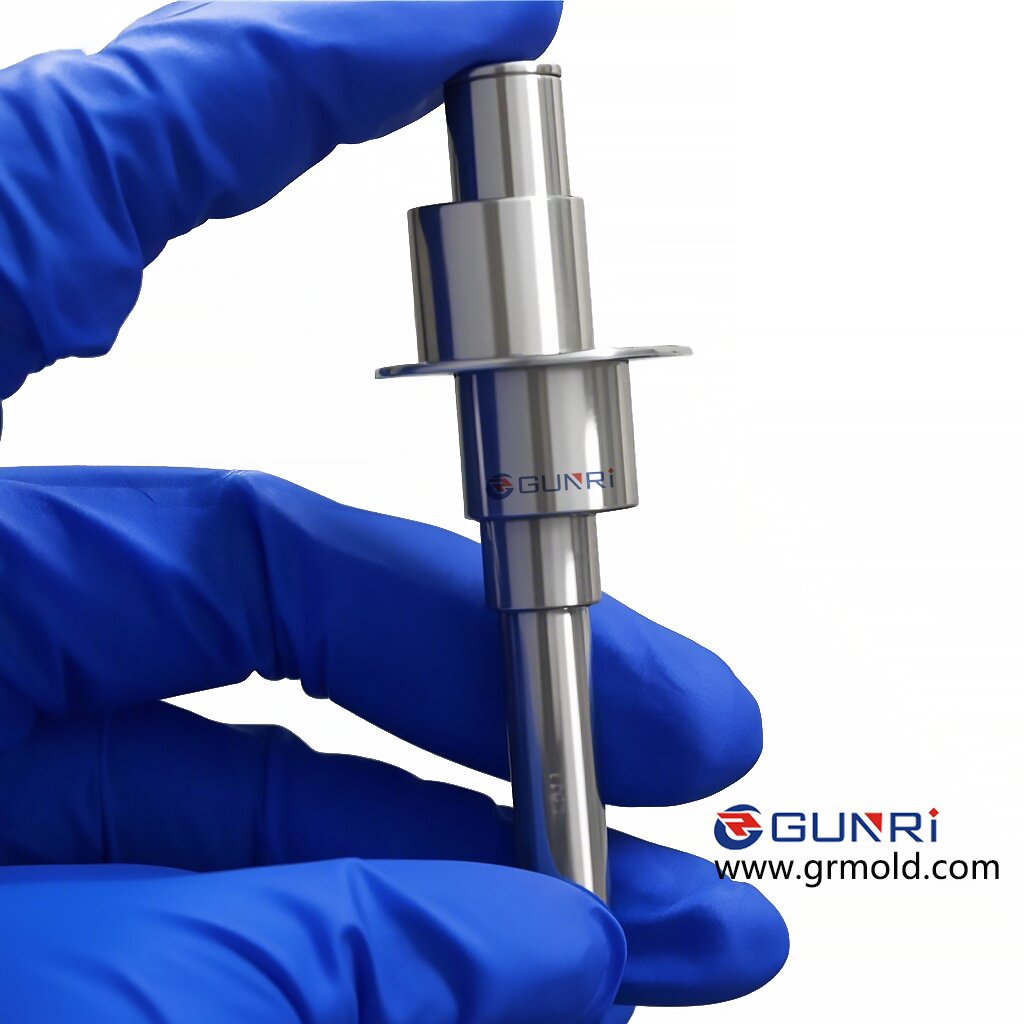
Role and Application of the Eccentric Shaft in RV Reducers
2.1 Functional Positioning
The eccentric shaft is located at the core of the RV reducer’s transmission system, bridging the input power source (e.g., a servo motor) and the cycloidal discs. Its primary roles include:
- Motion Conversion: Converting the input shaft’s pure rotational motion into eccentric orbital motion through its offset journal (eccentric section).
- Driving Cycloidal Discs: Transmitting this eccentric motion to the cycloidal discs, which then engage with the stationary needle bearing ring to achieve high-precision speed reduction.
- Load Distribution: Balancing forces across the reducer’s structure to minimize vibration and wear.
2.2 Key Applications
RV reducers with eccentric shafts are essential in:
- Industrial Robot Joints: Ensuring precise motion control in robotic arms (e.g., welding, assembly).
- CNC Machine Tools: Driving rotary tables or spindle adjustments.
- Aerospace Actuators: Controlling satellite antenna positioning or spacecraft mechanisms.
Procurement Considerations for Eccentric Shafts
When sourcing eccentric shafts for RV reducers, the following factors are critical to ensure performance, longevity, and cost-effectiveness:
3.1 Material Quality
- High-Strength Alloy Steel: The shaft must withstand cyclic loads and resist deformation. Common materials include SCM420H or 20CrMnTi, often carburized or induction-hardened.
- Surface Treatment: Anti-wear coatings (e.g., nitriding) enhance durability.
3.2 Precision and Tolerance
- Eccentricity Accuracy: The offset journal’s eccentricity tolerance should be within ±0.005 mm to ensure smooth engagement with cycloidal discs.
- Radial Runout: Must not exceed 0.01 mm to avoid vibration and noise.
- Surface Finish: A roughness of Ra ≤ 0.4 μm minimizes friction losses.
3.3 Heat Treatment Process
- Uniform Hardness: Core hardness (e.g., HRC 58-62) and surface hardness must be consistent to prevent premature fatigue or cracking.
- Stress Relief: Post-machining annealing reduces residual stress, improving dimensional stability.
3.4 Supplier Certification
- ISO 9001/14001: Ensures quality management and environmental compliance.
- Industry-Specific Standards: Certifications like AGMA (American Gear Manufacturers Association) or JIS B 1702 (Japanese Industrial Standards) validate precision.
3.5 Customization Requirements
- Tailored Dimensions: Match the reducer’s size (e.g., RV-40E, RV-110N) and load capacity.
- Compatibility Testing: Verify alignment with cycloidal discs and needle bearings through prototyping.
3.6 Quality Assurance
- Non-Destructive Testing (NDT): Use magnetic particle inspection or ultrasonic testing to detect internal flaws.
- Lifetime Testing: Simulate long-term operation (e.g., 10,000 hours) under load to validate fatigue resistance.
3.7 Cost vs. Performance
- Avoid prioritizing low-cost suppliers without proven track records in precision machining.
- Consider total lifecycle cost, including maintenance and downtime risks.
Conclusion
The eccentric shaft is the backbone of an RV reducer’s motion transmission system, enabling high torque, precision, and reliability. When procuring this component, prioritize material integrity, precision tolerances, certified suppliers, and rigorous testing protocols.
To request customized Eccentric Shaft solutions, please email us at milla@gunri.com.cn