Gas Spring vs. Die Spring in Die Sets
Die sets play a pivotal role in metalworking and fabrication processes, providing the necessary force and support to ensure precise cutting and shaping of materials. Two common types of springs used in die sets are gas springs and die springs. In this article, we will explore the characteristics, advantages, and applications of gas springs and die springs to facilitate a better understanding of their respective roles in die set operations.
Table of contents
Gas Springs: The Pneumatic Powerhouses
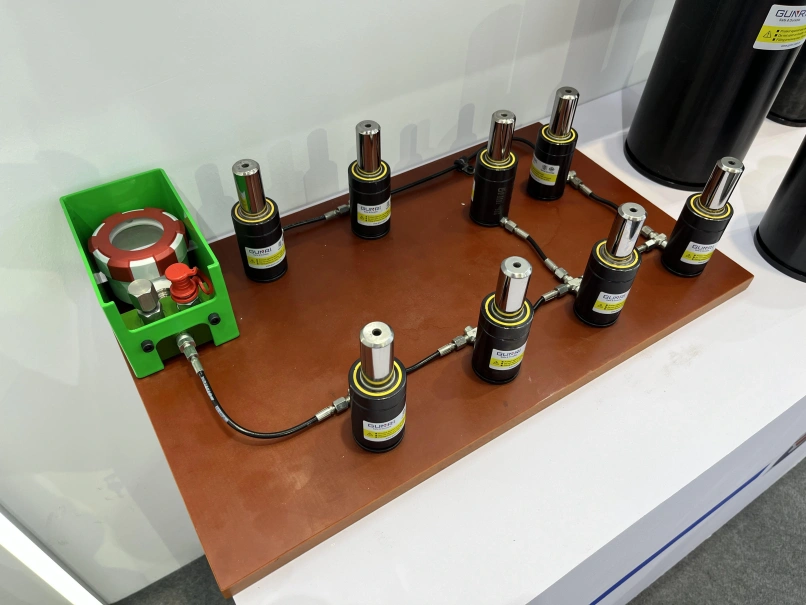
Gas springs, also known as gas struts or gas shocks, harness the power of compressed gas to provide controlled force in die sets. These springs consist of a piston and cylinder filled with pressurized nitrogen gas. When the gas is compressed, it exerts force on the piston, creating a linear motion. Gas springs offer several advantages in die sets:
1. Adjustability:
Gas springs provide the flexibility of adjusting the force applied by altering the gas pressure. This adjustability is advantageous when working with varying materials or when fine-tuning the die set for different tasks.
2. Smooth Operation:
The controlled and smooth motion of gas springs contributes to precision in die set operations. This feature is particularly beneficial in applications where consistent force is crucial for achieving high-quality cuts and shapes.
3. Space Efficiency:
Gas springs are often more compact than traditional mechanical springs, making them suitable for die sets with limited space. Their compact design allows for efficient use of space within the die set assembly.
4. Reduced Vibration:
The gas-filled nature of these springs minimizes vibration during operation, contributing to a quieter and more stable working environment. Reduced vibration is especially valuable when working with delicate materials or intricate designs.
Die Springs: Mechanical Workhorses
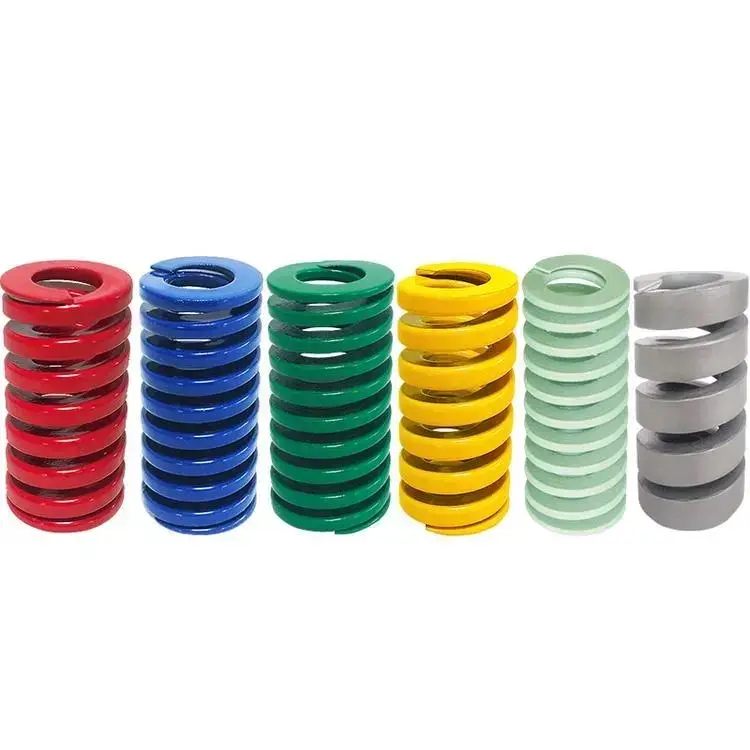
Die springs, on the other hand, are mechanical springs made of hardened and tempered steel. They are specifically designed for heavy-duty applications in die sets, providing reliable and consistent force. Die springs offer unique characteristics that distinguish them in die set operations:
1. High Load Capacity:
Die springs are known for their robustness and ability to handle heavy loads. This makes them suitable for applications where substantial force is required to cut or shape materials, ensuring durability and longevity.
2. Pre-Set Load Levels:
Die springs are available in various load levels, allowing for precise selection based on the requirements of the die set operation. This pre-set load capacity ensures uniform performance and reliable results.
3. Durability:
The materials used in die springs, typically alloyed steel, provide high resistance to wear and deformation. This durability is essential in die set applications where the springs undergo repetitive and demanding tasks.
4. Cost-Effectiveness:
Die springs are often more cost-effective than gas springs, making them a preferred choice for applications where budget considerations play a significant role.
Choosing the Right Spring for the Job
The choice between gas springs and die springs in die sets ultimately depends on the specific requirements of the application. Gas springs offer versatility and adjustability, making them suitable for tasks that demand precision and control. On the other hand, die springs excel in heavy-duty applications, providing consistent force and durability.
In conclusion, understanding the characteristics and advantages of gas springs and die springs is crucial for optimizing die set performance. Whether it’s achieving precision in intricate designs or handling heavy loads with reliability, the right choice between gas springs and die springs can significantly impact the efficiency and effectiveness of die set operations.