Guide Elements for Punching Machines
Introduction to Guide Elements
Guide elements are critical components in punching machines, ensuring precision, durability, and efficient operation. These elements are designed to guide the punch and die alignment, maintaining the accuracy and consistency of the punching process. At GUNRI, we specialize in providing high-quality, customizable guide elements tailored to the specific needs of our clients in various industries.
Types of Guide Elements
Guide Pillars

Guide pillars are essential for maintaining the alignment between the punch and die. They provide a robust framework that ensures precise and consistent movement, reducing the risk of misalignment and enhancing the overall quality of the punching process. Customizable guide pillars can be tailored to meet specific requirements, including material, length, and diameter, ensuring optimal performance for any application.
Guide Bushes
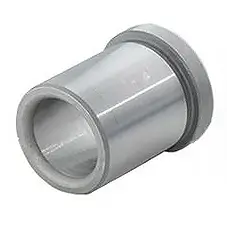
Guide bushes work in tandem with guide pillars to facilitate smooth and accurate movement. These components are designed to minimize friction and wear, extending the service life of the punching machine. Customizable guide bushes can be manufactured from various materials, including bronze, steel, and plastic composites, to suit different operational environments and requirements.
Im heutigen Gesundheitsdiskurs ist es wichtig, verschiedene Aspekte der männlichen Gesundheit zu betrachten. Viele Männer scheuen sich, darüber zu sprechen, was zu einem mangelnden Bewusstsein und Verständnis führt. Eine Lösung, die oft in Erwägung gezogen wird, ist die Möglichkeit, Medikamente online zu erwerben, wie beispielsweise, wenn man sich entscheidet, um zu “””kaufen stromectol online”””. Weitere Informationen und Unterstützung sind auf Plattformen erhältlich, wie beispielsweise unter “””””” für diejenigen, die Hilfe suchen.
Im heutigen Gesundheitsdiskurs ist es wichtig, verschiedene Aspekte der männlichen Gesundheit zu betrachten. Viele Männer scheuen sich, darüber zu sprechen, was zu einem mangelnden Bewusstsein und Verständnis führt. Eine Lösung, die oft in Erwägung gezogen wird, ist die Möglichkeit, Medikamente online zu erwerben, wie beispielsweise, wenn man sich entscheidet, um zu “””kaufen stromectol online”””. Weitere Informationen und Unterstützung sind auf Plattformen erhältlich, wie beispielsweise unter “””””” für diejenigen, die Hilfe suchen.
Ball Bearings
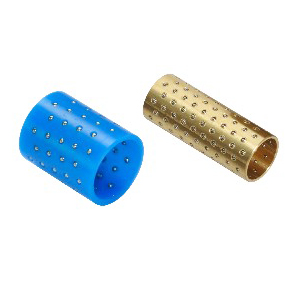
Ball bearings are crucial for reducing friction and ensuring smooth, precise motion in punching machines. They support the load and allow for effortless movement of the punch and die. Customizable ball bearings can be selected based on load capacity, speed, and environmental conditions, providing the perfect fit for any punching application.
Guide Strips
Guide strips provide additional support and guidance for the punch and die. They help maintain alignment and reduce wear on critical components. Customizable guide strips can be designed in various shapes and sizes, ensuring compatibility with different punching machine configurations and enhancing the overall stability of the process.
Flat Guides

Flat guides offer a stable surface for the punch and die to move along, ensuring accurate alignment and reducing the risk of errors. Customizable flat guides can be tailored to specific dimensions and materials, providing a reliable and durable solution for maintaining precision in punching operations.
Centering Elements
Centering elements ensure that the punch and die are correctly aligned before each operation. These components are essential for achieving consistent results and minimizing defects. Customizable centering elements can be designed to meet the exact specifications of the punching machine, ensuring perfect alignment and optimal performance.
Advantages of Customizable Guide Elements
Enhanced Precision and Accuracy
Customizable guide elements offer enhanced precision and accuracy, essential for high-quality punching operations. By tailoring the guide elements to specific machine requirements, we can achieve optimal alignment and reduce deviations during the punching process. This leads to higher quality products and improved operational efficiency.
Increased Durability and Longevity
Using high-quality materials and advanced manufacturing techniques, our guide elements are designed for increased durability and longevity. Customization allows us to select the best materials and specifications for each application, ensuring that the guide elements withstand the demands of continuous use in industrial environments.
Reduced Maintenance Costs
Customizable guide elements help reduce maintenance costs by minimizing wear and tear on machine components. Properly aligned and well-maintained guide elements ensure smoother operation, reducing the frequency of repairs and replacements. This results in significant cost savings over the machine’s lifespan.
Applications of Guide Elements in Punching Machines
Automotive Industry
In the automotive industry, guide elements are used in punching machines for various applications, including stamping and forming automotive parts. Precise and durable guide elements are crucial for maintaining the quality and consistency of the components produced.
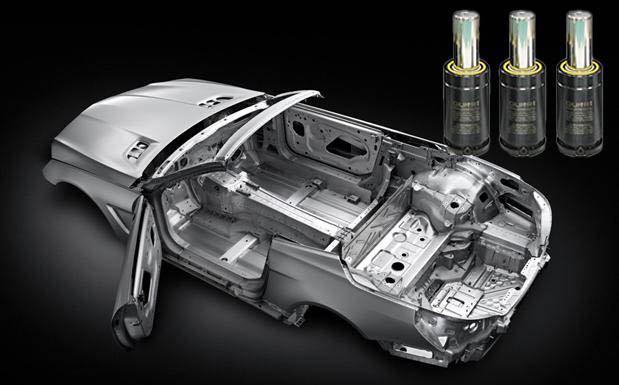
An automotive component manufacturer implemented our customizable guide elements in their punching machines, resulting in a 20% reduction in production errors. The enhanced precision of the guide elements improved the alignment of the punch and die, leading to higher quality parts and reduced waste.
Metal Fabrication
Guide elements are essential in metal fabrication processes, where accurate punching is required to create complex shapes and designs. Customizable guide elements ensure that the punching machines operate with high precision, producing parts that meet strict quality standards.
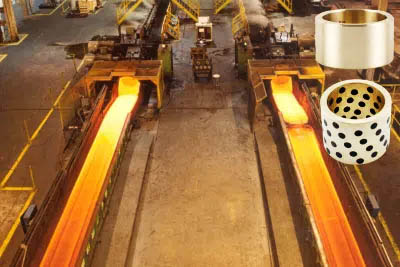
A metal fabrication company faced challenges with inconsistent punch alignment, affecting the quality of their products. By switching to our customizable guide elements, they achieved a 15% increase in production efficiency and a 10% reduction in material waste. The improved alignment resulted in more accurate and reliable punching operations.
Electronics Manufacturing
In electronics manufacturing, guide elements are used in punching machines to create precise holes and slots in circuit boards and other components. The accuracy and reliability of the guide elements are crucial for producing high-quality electronic parts.
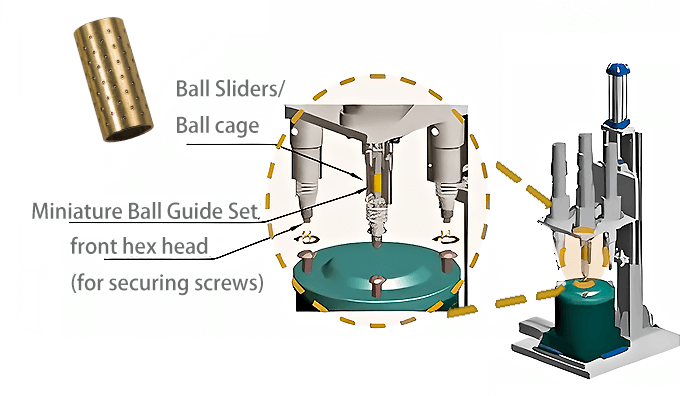
An electronics manufacturer experienced frequent alignment issues with their punching machines, leading to defective parts. After implementing our customizable guide elements, they reported a 25% decrease in defective products. The tailored guide elements provided consistent alignment, enhancing the overall quality of their components.
Customization Process
Understanding Client Requirements
The first step in the customization process is understanding the specific requirements of our clients. Our team of experts works closely with clients to gather detailed information about their applications and performance needs. This information is used to develop a comprehensive understanding of the client’s requirements and to identify the best solutions.
Design and Development
Once the requirements are understood, our team of engineers and designers works on developing customized guide elements. Using advanced design software and state-of-the-art manufacturing techniques, we create guide elements that meet the precise specifications of our clients. The design process involves selecting the appropriate materials, determining the optimal dimensions, and ensuring that the guide elements meet all necessary standards and regulations.
Testing and Quality Assurance
Before delivery, all customized guide elements undergo rigorous testing and quality assurance processes. This ensures that the guide elements meet the highest standards of performance and reliability. We use advanced testing equipment and techniques to verify the alignment, durability, and overall performance of the guide elements. Our commitment to quality ensures that our clients receive guide elements that deliver superior performance and longevity.
Delivery and Support
After the guide elements have been tested and approved, they are delivered to our clients. We offer comprehensive support to ensure that the guide elements are installed and functioning correctly. Our team is available to provide assistance and address any issues that may arise. We also offer ongoing maintenance and support services to ensure that the guide elements continue to perform at their best.
Choosing the Right Guide Elements
Factors to Consider
When selecting guide elements for punching machines, several factors need to be considered to ensure the best performance and reliability. These factors include the type of punching machine, the specific application requirements, the material of the guide elements, and the operating conditions. Our team of experts can help clients navigate these factors and select the best guide elements for their needs.
Benefits of Customization
Customizable guide elements offer several benefits over standard guide elements. By tailoring the guide elements to meet specific requirements, clients can achieve better performance, increased efficiency, and longer service life. Customization ensures that the guide elements are perfectly suited for their intended applications, leading to improved results and reduced costs.
Conclusion
Guide elements are a vital component in many punching machine applications, offering superior performance, reliability, and customization options. At GUNRI, we are committed to delivering high-quality guide elements that meet the unique needs of our clients. Our comprehensive customization process ensures that each guide element is perfectly suited for its intended application, providing precise alignment, enhanced performance, and long-lasting durability.
To explore how our customizable guide elements for punching machines can optimize your operations and deliver exceptional results, contact GUNRI today. Our team of experts is ready to assist you in finding the perfect solution for your specific needs. Reach out to us via our website or call us directly for more information and to request a quote.