How Nitrogen Gas Springs Reduce Maintenance Costs and Downtime Risks for Frequent Mold Damage
Understanding the Problem of Frequent Mold Damage
1.Common Causes of Mold Damage
Excessive pressure is a prevalent culprit behind mold damage. During the manufacturing process, if the pressure exerted on the mold exceeds its designed capacity, it can cause severe stress on the mold structure. For instance, in injection molding, when the injection pressure is set too high to force the molten material into the mold cavity, the internal components of the mold may experience uneven stress distribution. This can lead to cracks forming in the mold walls or deformation of the core and cavity surfaces over time.
Wear and tear is another significant factor. Continuous use of the mold subjects it to friction and mechanical stress. Every time the mold is opened and closed, or when the molded parts are ejected, the surfaces of the mold rub against each other. In die-casting molds, the repeated impact of the molten metal hitting the mold surface can gradually erode the material, causing the surface to become rough and dimensions to change. This wear not only affects the quality of the molded products but also weakens the mold structure, making it more prone to failure.
Improper installation also plays a role in mold damage. If the mold is not installed correctly, it can lead to misalignment or uneven loading. For example, in a stamping mold, if the upper and lower dies are not properly aligned during installation, the force applied during stamping will be uneven. This can cause one side of the mold to bear more stress than the other, resulting in premature wear and potential cracking.
Material fatigue is a long-term cause of mold damage. Over an extended period of use, the mold material undergoes repeated stress cycles. Even if the stress levels are within the normal operating range, the cumulative effect of these cycles can cause the material to lose its strength and ductility. Eventually, micro-cracks start to form, which can grow and lead to catastrophic failure of the mold. This is especially true for molds made of high-strength alloys that are exposed to cyclic loading in high-volume production environments.
2.Impact of Frequent Mold Damage
Frequent mold damage exacts a heavy toll on manufacturing operations. Firstly, maintenance costs skyrocket. When molds are damaged often, there are expenses for repairs, replacement parts, and the labor of skilled technicians. For example, a plastics manufacturing company found that due to regular mold wear and tear, they were spending an additional $50,000 annually on mold repairs compared to when the molds were in better condition.
Production downtime is another significant consequence. Every time a mold is damaged, production has to halt. In a car parts factory, a mold used for casting engine components broke down unexpectedly. This led to a three-day production stoppage, resulting in a loss of hundreds of units of output and potential revenue.
Potential quality issues also arise. Damaged molds can produce parts with inconsistent dimensions, surface defects, or structural weaknesses. A toy manufacturing firm noticed that after a mold started showing signs of wear, the toys produced had rough edges and improper fits. This led to customer complaints and a hit to the company’s reputation. All these impacts highlight the urgent need for solutions like nitrogen gas springs to mitigate mold damage and its associated problems.
Introduction to Nitrogen Gas Springs
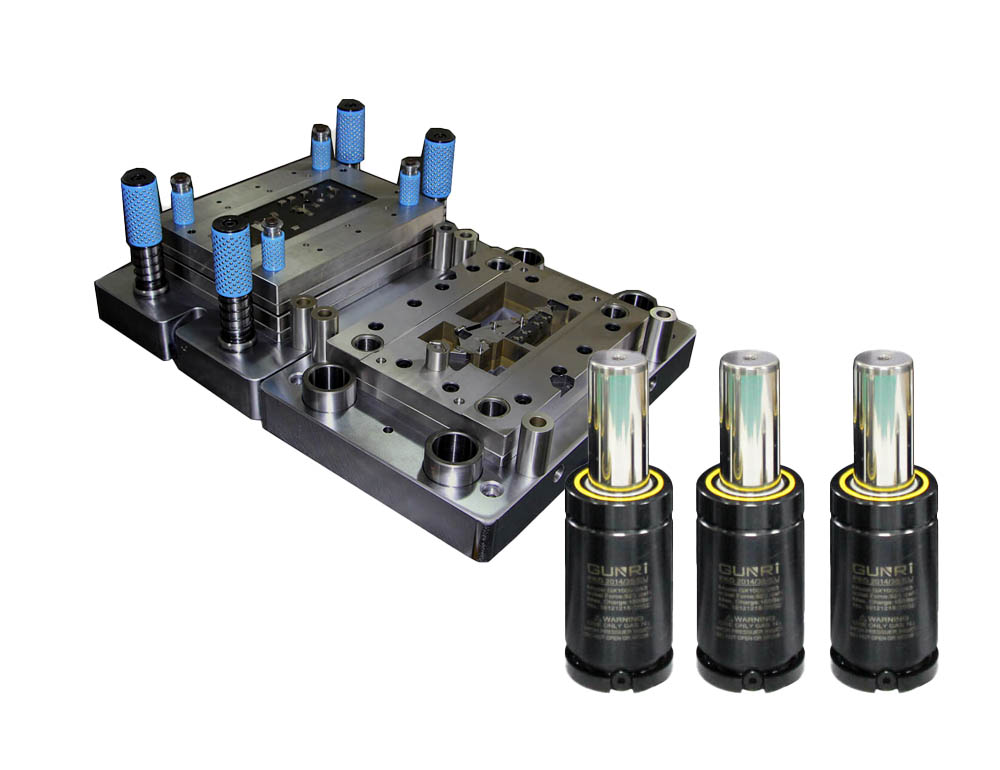
1.What are Nitrogen Gas Springs
Nitrogen gas springs operate on a principle distinct from traditional mechanical springs. At their core, they utilize the compressibility of nitrogen gas, which is sealed within a cylinder. This gas acts as the elastic medium, storing and releasing energy when subjected to external forces.
The basic structure of a nitrogen gas spring consists of a cylinder, a piston, and a rod. The cylinder houses the nitrogen gas under high pressure. The piston divides the cylinder into two chambers, with the nitrogen gas in one chamber. When an external force is applied to the rod, the piston moves, compressing the nitrogen gas. This compression stores energy, much like a traditional spring being compressed.
Compared to traditional springs, nitrogen gas springs offer several unique features. One key advantage is their ability to provide a more consistent and adjustable force. Traditional springs have a fixed spring rate, meaning the force they exert changes linearly with the displacement. In contrast, nitrogen gas springs can be adjusted to provide a constant force over a range of displacements or a custom force profile. This makes them ideal for applications where precise force control is crucial. Additionally, nitrogen gas springs can handle higher loads in a more compact size, offering greater efficiency and performance in space-constrained environments.
2.Working Mechanism of Nitrogen Gas Springs
The operation of nitrogen gas springs is a fascinating process that involves the interaction of nitrogen gas and mechanical components. When a load is applied to the rod of the nitrogen gas spring, the piston begins to move within the cylinder. As the piston moves, it compresses the nitrogen gas in the chamber. Nitrogen gas, being highly compressible, stores the energy from the applied load.
This stored energy can be thought of as potential energy, similar to how a traditional spring stores energy when compressed. When the external load is removed, the compressed nitrogen gas expands, pushing the piston back in the opposite direction. This expansion of the nitrogen gas releases the stored energy, causing the rod to extend and return to its original position.
The mechanical components play crucial roles in this process. The cylinder provides a sealed environment for the nitrogen gas, ensuring that it remains under pressure. The piston, with its precise fit within the cylinder, effectively transfers the force from the rod to the nitrogen gas and vice versa. The rod is the part that interacts directly with the external load or the object being actuated.
[Here you can insert a simple diagram showing a nitrogen gas spring with labeled parts like cylinder, piston, rod, and the chamber with nitrogen gas. The diagram should illustrate the movement of the piston when the rod is pushed in (compression) and when it is released (expansion).] This working mechanism allows nitrogen gas springs to provide a smooth and reliable source of force, making them suitable for a wide range of applications in mold systems.
How Nitrogen Gas Springs Reduce Maintenance Costs
1.Durability and Longevity
Nitrogen gas springs are engineered with durability and longevity in mind, making them a reliable choice for reducing the frequency of replacements. Their construction materials and design features contribute significantly to their extended lifespan. For instance, the cylinders of nitrogen gas springs are often made from high-strength alloys or corrosion-resistant materials. This not only protects the internal components from damage but also ensures that the gas remains sealed under pressure for an extended period.
A case study from a metal stamping company demonstrates the impressive durability of nitrogen gas springs. Prior to using nitrogen gas springs, the company was replacing traditional mechanical springs every three months due to wear and tear. After switching to nitrogen gas springs, they found that the springs lasted for over two years without any significant degradation in performance. This represents a substantial reduction in replacement costs and downtime associated with spring changes.
The design of nitrogen gas springs also contributes to their long lifespan. The use of advanced seals and piston designs minimizes internal leakage, ensuring consistent performance over time. Additionally, the ability to adjust the force output of nitrogen gas springs allows for optimal operation under various conditions, reducing stress on the spring and extending its life. Overall, these features make nitrogen gas springs a cost-effective solution for mold applications, as they reduce the need for frequent replacements and associated maintenance costs.
2.Reduced Wear and Tear
Nitrogen gas springs play a pivotal role in minimizing wear and tear on molds by offering a more stable and consistent force. Traditional springs often suffer from variations in force output due to factors like material fatigue and manufacturing tolerances. In contrast, nitrogen gas springs maintain a steady force throughout their operation, which significantly reduces the stress placed on mold components.
For example, in a plastic injection molding process, the injection of molten plastic into the mold cavity requires a precise and consistent force to ensure proper filling and accurate part formation. With a nitrogen gas spring, the force applied during the injection phase remains constant, preventing uneven pressure distribution within the mold. This stability reduces the likelihood of mold walls experiencing excessive stress, which can lead to wear and deformation over time.
Another instance is in die-casting operations. The high-pressure injection of molten metal into the die can cause substantial wear on the die surfaces. Nitrogen gas springs, with their consistent force, help to evenly distribute the pressure during the casting process. This results in less wear on the die’s core and cavity surfaces, as well as on the ejection mechanisms. By minimizing wear and tear, nitrogen gas springs not only extend the lifespan of mold components but also contribute to the overall quality and consistency of the molded products. This ultimately leads to reduced maintenance costs and fewer production interruptions due to mold damage.
3.Easier Maintenance
Maintaining nitrogen gas springs is a relatively straightforward task, offering significant advantages over traditional springs. Routine inspections of nitrogen gas springs typically involve simple visual checks. Technicians can easily examine the exterior of the cylinder for any signs of damage, such as dents or scratches, which could potentially lead to gas leakage. Checking the connection points of the rod and piston for any signs of looseness is also a quick and uncomplicated process.
Basic maintenance procedures mainly consist of ensuring the seals are in good condition and that the nitrogen gas pressure remains within the recommended range. This often requires only a pressure gauge to verify the pressure, and in the rare case of a minor pressure adjustment, it can be done with simple tools.
In contrast, traditional springs demand more intricate maintenance. They often need to be disassembled for a thorough inspection, which can be time-consuming and requires specialized skills. Traditional springs are also more prone to issues like rust and corrosion, necessitating regular cleaning and lubrication. These additional maintenance steps not only increase the time and effort required but also the associated costs. With nitrogen gas springs, their simpler maintenance requirements translate to less downtime for maintenance activities, allowing for more continuous and efficient production.
Minimizing Downtime Risks with Nitrogen Gas Springs
1.Quick Installation and Replacement
Installing and replacing nitrogen gas springs is a breeze, making them a boon for minimizing production downtime. Their design allows for a relatively straightforward process, even in the midst of a busy manufacturing environment.
The installation process is often quick due to the modular nature of nitrogen gas springs. They are typically designed to fit standard mounting points on molds, which means that technicians can easily align and attach them without the need for complex modifications. For example, in many stamping molds, the nitrogen gas springs can be inserted into pre-drilled holes and secured with simple fasteners. This plug-and-play nature reduces the time spent on installation compared to more complex components.
When it comes to replacement, nitrogen gas springs also shine. In the event of a malfunction or routine replacement, the process can be completed rapidly. Since they are self-contained units, swapping out a worn-out spring for a new one can be done without having to disassemble large portions of the mold.
For efficient installation, here are some practical tips. First, ensure that all the necessary tools are on hand before starting the installation. This includes wrenches, screwdrivers, and any specialized tools for handling the nitrogen gas pressure if required. Second, carefully read the installation instructions provided by the manufacturer. These instructions will detail the correct orientation and torque settings for the fasteners. Finally, perform a quick check of the new spring’s functionality before fully installing it. This can involve a simple pressure test to ensure that the spring is operating as expected. By following these steps, manufacturers can enjoy the benefits of quick installation and replacement, keeping production downtime to a minimum.
2.Predictable Performance
The consistent performance of nitrogen gas springs is a game-changer when it comes to manufacturing planning and scheduling. Unlike traditional springs that may experience fluctuations in force output over time, nitrogen gas springs maintain a stable and predictable performance throughout their lifespan. This reliability allows manufacturers to better anticipate production needs and allocate resources effectively, minimizing the risk of unexpected downtime.
A case in point is a consumer goods manufacturing company that produces plastic containers. Before adopting nitrogen gas springs in their injection molding machines, they often faced production disruptions due to inconsistent spring performance. Traditional springs would gradually lose their elasticity, leading to variations in the force applied during the molding process. This resulted in defective products and unplanned machine stoppages for spring replacements.
After switching to nitrogen gas springs, the company witnessed a significant improvement in production stability. The consistent force provided by the nitrogen gas springs ensured that each plastic container was molded to the exact specifications, reducing the number of defective products. Moreover, the predictable performance of the springs allowed the company to schedule maintenance and replacements in advance, based on the expected lifespan of the springs. As a result, the company was able to reduce unexpected downtime by 40%, leading to a substantial increase in productivity and cost savings.
In addition to improving production efficiency, the predictable performance of nitrogen gas springs also enables manufacturers to optimize their inventory management. By knowing exactly how long a spring will last and when it needs to be replaced, companies can maintain a lean inventory of spare parts, reducing the cost of inventory holding. Overall, the consistent performance of nitrogen gas springs provides manufacturers with the confidence and flexibility they need to operate their production lines smoothly and efficiently.
3.Compatibility and Adaptability
Nitrogen gas springs exhibit remarkable compatibility with a diverse range of molds and manufacturing processes, making them a versatile solution across industries. In the realm of injection molding, nitrogen gas springs can be seamlessly integrated into molds of various sizes and complexities. Whether it’s a small, precision mold for producing intricate electronic components or a large-scale mold for manufacturing automotive parts, nitrogen gas springs can be tailored to meet the specific force and stroke requirements.
For die-casting molds, nitrogen gas springs are equally adaptable. They can withstand the high pressures and temperatures associated with die-casting processes, providing reliable force control during the injection and ejection phases. This compatibility ensures that the die-casting process runs smoothly, minimizing the risk of mold damage and production interruptions.
In stamping and forming operations, nitrogen gas springs can be easily incorporated into the mold design. They offer the flexibility to adjust the force according to the material being stamped or formed, whether it’s a thin sheet of metal or a thicker, more robust material.
Moreover, nitrogen gas springs are compatible with different manufacturing processes, including automated production lines. Their modular design and standardized mounting interfaces allow for easy integration into existing equipment, enabling manufacturers to upgrade their systems without major modifications. This adaptability reduces the downtime associated with equipment changes and compatibility issues, ensuring a seamless transition and continuous production. Overall, the compatibility and adaptability of nitrogen gas springs make them an invaluable asset in modern manufacturing.
Case Studies of Successful Implementation
1.Case Study 1: Automotive Industry
A leading automotive parts manufacturer was grappling with high mold maintenance costs and frequent downtime. Their molds, used for manufacturing components like engine brackets and transmission housings, were suffering from rapid wear and tear due to the high-pressure forming processes. Traditional springs were unable to provide consistent force, leading to uneven stress distribution and premature mold failure.
Upon adopting nitrogen gas springs, the results were remarkable. The consistent force provided by these springs reduced wear on the molds by 60%, as measured by the rate of surface degradation. This led to a significant extension in mold lifespan.
In terms of cost savings, the company witnessed a reduction of approximately $150,000 annually in mold repair and replacement costs. Downtime also decreased substantially. Before the switch, unplanned production halts due to mold issues occurred on average 10 times a year, each lasting around 2 days. After implementing nitrogen gas springs, the number of unplanned stoppages dropped to just 3 times a year, with each incident lasting only half a day.
Productivity soared as a result. The company was able to increase their annual production output by 12%, translating into a significant boost in revenue. This case study clearly demonstrates the transformative impact of nitrogen gas springs in the automotive manufacturing sector.
2.Case Study 2: Electronics Manufacturing
An electronics manufacturing company specializing in producing small, intricate components for smartphones faced numerous challenges. Their molds, used for precision injection molding of parts like connectors and sensors, were highly susceptible to damage. The delicate nature of the components and the high precision required meant that even minor variations in force during the molding process could lead to defective products. Traditional springs were unable to maintain the consistent and precise force needed, resulting in a high rejection rate of up to 15%.
To address these issues, the company decided to implement nitrogen gas springs. These springs provided a stable and adjustable force, ensuring that each component was molded with the exact specifications. The ability to fine-tune the force according to the specific requirements of each part was a game-changer.
As a result, the rejection rate dropped significantly to just 3%. This not only reduced waste but also saved costs associated with rework and scrap. The molds, now subject to less stress and wear, lasted longer, reducing the frequency of mold replacements. The company also experienced a 20% increase in production efficiency as the molds could operate more smoothly and consistently. Overall, nitrogen gas springs proved to be a valuable solution in the electronics manufacturing environment, enhancing both quality and productivity.
Best Practices for Using Nitrogen Gas Springs
1.Selection and Sizing
Selecting the appropriate nitrogen gas spring for your mold application is crucial to ensure optimal performance and longevity. Here are some key factors to consider:
Factor | Consideration |
Load Capacity | Determine the maximum load the spring will need to support. This depends on the forces exerted during the molding process, such as the pressure of injecting molten material or the force required for ejection. Ensure the chosen spring has a load capacity that exceeds the expected maximum load to prevent premature failure. |
Stroke Length | The stroke length is the distance the spring will travel during operation. It should be sufficient to accommodate the movement required in the mold, such as the opening and closing of the mold or the ejection of the molded part. Measure the required stroke length accurately and select a spring with an appropriate stroke length to avoid any interference or insufficient movement. |
Pressure Requirements | Consider the pressure range within which the spring will operate. Different applications may require specific pressure levels to achieve the desired force and performance. Make sure the nitrogen gas spring you choose can withstand the expected pressure and provide the necessary force output. |
Mounting Options | Check the available mounting options for the nitrogen gas spring. Ensure that it can be easily installed and integrated into your mold design. Consider factors such as the mounting holes, brackets, or adapters required for proper installation. |
Environmental Conditions | Take into account the operating environment of the mold. If the mold is exposed to high temperatures, corrosive substances, or other harsh conditions, select a nitrogen gas spring that is suitable for such environments. Some springs are designed with special materials or coatings to withstand extreme conditions. |
By carefully considering these factors and using the provided checklist, you can select the right nitrogen gas spring for your specific mold application. This will help ensure reliable performance, reduce maintenance costs, and minimize downtime risks. Remember to consult the manufacturer’s specifications and recommendations for further guidance.
2.Installation and Setup
Proper installation and setup of nitrogen gas springs are essential for their optimal performance. Here is a step-by-step guide:
Step 1: Safety Precautions
Before starting, always wear appropriate safety gear, such as safety glasses and gloves. Nitrogen gas springs are under pressure, and any mishandling could cause injury. Ensure the power source to the mold is turned off to prevent accidental activation during installation.
Step 2: Prepare the Workspace
Clear the area around the mold of any debris or tools that could interfere with the installation. Have all the necessary tools ready, such as wrenches, screwdrivers, and a pressure gauge if pressure adjustment is required.
Step 3: Alignment
Carefully align the nitrogen gas spring with the mounting points on the mold. Most springs are designed to fit standard mounting holes. Use alignment pins or guides, if available, to ensure perfect alignment. Misalignment can cause uneven stress distribution and affect the spring’s performance.
Step 4: Installation
Insert the spring into the mounting holes and secure it using the provided fasteners. Tighten the fasteners to the recommended torque settings specified by the manufacturer. Over-tightening can damage the spring or the mold, while under-tightening may cause the spring to loosen during operation.
Step 5: Pressure Check and Adjustment (if needed)
Use a pressure gauge to check the nitrogen gas pressure in the spring. If the pressure is not within the recommended range, carefully adjust it using the appropriate tools. This should be done following the manufacturer’s instructions precisely.
[Here you can insert a simple diagram showing the installation process, highlighting the alignment of the spring with the mold, the use of fasteners, and the pressure check point.] By following these steps, you can ensure a proper installation and setup of nitrogen gas springs, maximizing their benefits and minimizing potential issues.
3.Maintenance and Monitoring
To ensure the optimal performance of nitrogen gas springs, a regular maintenance schedule and monitoring procedures are essential.
For the maintenance schedule, conduct a visual inspection at least once a month. Check for any external damage like scratches or dents on the cylinder, as these could lead to gas leakage. Inspect the connection points of the rod and piston for signs of looseness. Every six months, perform a more in-depth check, including verifying the nitrogen gas pressure with a pressure gauge. If the pressure is outside the recommended range, adjust it according to the manufacturer’s guidelines.
Monitoring procedures should include keeping track of the spring’s performance over time. Note any changes in the force output, such as a decrease in the ejection force during the molding process. This could indicate internal issues.
When it comes to troubleshooting common issues, if there is a sudden drop in force, it might be due to a gas leak. Check the seals carefully for any signs of leakage. If the spring seems to be sticking or not moving smoothly, it could be due to debris or contamination. In this case, clean the spring gently according to the manufacturer’s instructions. By following these maintenance and monitoring steps, and being able to troubleshoot common problems, manufacturers can keep nitrogen gas springs operating at their best, reducing the risk of mold damage and production disruptions.
Conclusion
1.Summary of Key Points
This article delved into the problem of frequent mold damage, its causes, impacts, and how nitrogen gas springs offer effective solutions. Mold damage often results from excessive pressure, wear and tear, improper installation, and material fatigue, leading to increased maintenance costs, production downtime, and quality issues.
Nitrogen gas springs operate on the compressibility of nitrogen gas, offering unique features like consistent and adjustable force, and higher load capacity in a compact size compared to traditional springs. Their durability and longevity reduce replacement needs, as seen in case studies where they lasted much longer than traditional counterparts. By providing a stable force, they minimize wear and tear on molds, extending the lifespan of mold components.
Maintenance of nitrogen gas springs is simpler, involving basic visual checks and pressure verification. Their quick installation and replacement, predictable performance, and compatibility with various molds and processes further minimize downtime risks. Case studies from the automotive and electronics industries demonstrated significant cost savings, productivity improvements, and quality enhancements after adopting nitrogen gas springs. In summary, nitrogen gas springs are a valuable asset in reducing maintenance costs and downtime risks associated with mold damage.
2.Future Trends and Considerations
The future of nitrogen gas spring technology holds exciting prospects for enhancing mold performance and reliability. One emerging trend is the integration of smart sensors within nitrogen gas springs. These sensors can monitor real-time parameters such as pressure, temperature, and force output. By collecting this data, manufacturers can gain valuable insights into the spring’s performance and predict potential issues before they occur. This proactive approach to maintenance can further minimize downtime and optimize mold operation.
Another trend is the development of more lightweight yet robust materials for nitrogen gas spring construction. This not only reduces the overall weight of the mold but also improves energy efficiency. Additionally, advancements in manufacturing techniques may enable the production of nitrogen gas springs with even more precise tolerances and complex geometries, allowing for better customization to specific mold requirements.
To stay ahead in manufacturing processes, readers should keep an eye on these technological advancements. Collaborating with suppliers who are at the forefront of innovation can provide access to the latest nitrogen gas spring solutions. Additionally, investing in employee training to understand and utilize these new technologies will be crucial. By embracing these future trends, manufacturers can continue to improve mold performance, reduce costs, and maintain a competitive edge in the market.