Nitrogen Gas Springs for Dies vs Die Springs: Which Is Right for Your Applications?
When it comes to optimizing manufacturing processes, understanding the differences between Nitrogen Gas Springs for Dies vs Die Spring is crucial for selecting the right components. Both types of springs serve essential roles in various applications, but their functionalities, design characteristics, and performance can vary significantly. In this blog post, we will explore these differences in detail, helping you make an informed choice for your specific needs. Whether you are looking for efficiency, durability, or cost-effectiveness, this comprehensive comparison will guide you toward the best solution for your manufacturing operations.
Table of contents
Definition and Functionality
Nitrogen Gas Springs for Dies are favored for applications requiring high force output and rapid actuation, while Die Springs provide stability and durability in high-load scenarios. Understanding these differences helps in selecting the right spring type for your specific needs.
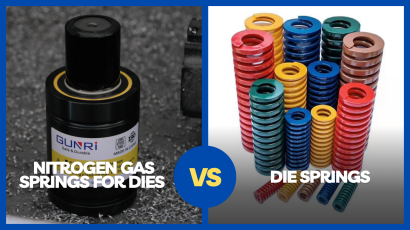
Nitrogen Gas Springs for Dies
Nitrogen gas springs are hydraulic components that use nitrogen gas to provide force and motion in various applications, particularly in die and mold setups. These springs consist of a cylinder filled with nitrogen gas, which acts as a compressible medium. When the piston inside the cylinder is compressed, the nitrogen gas is pressurized, allowing for a controlled and efficient release of force when needed.
Functionality:
- High Force Output: Nitrogen gas springs can deliver significant force with minimal space, making them ideal for compact applications.
- Adjustable: The force output can be adjusted based on the nitrogen gas pressure, providing flexibility for different operational requirements.
- Rapid Response: They offer quick and precise movement, making them suitable for applications that require high-speed actuation.
Die Springs
Die springs are mechanical springs designed for applications where high load and frequent cycles are involved. Typically made from high-carbon steel or other durable materials, die springs are available in various shapes and sizes, including compression, tension, and torsion forms.
Functionality:
- Stability Under Load: Die springs maintain their shape and performance under heavy loads, which is crucial in die-casting and stamping processes.
- Durability: They are engineered to withstand high fatigue and can be used in applications with repetitive cycles without losing their effectiveness.
- Variety: Die springs come in different spring rates and sizes, allowing for customization to meet specific operational needs.
Design and Construction
Nitrogen Gas Springs for Dies feature a more complex design with a sealed gas chamber that allows for adjustable force, while Die Springs have a simpler coil design that excels in durability and load-bearing capacity.
Nitrogen Gas Springs for Dies
Design:
Nitrogen gas springs are designed with a sealed cylinder that contains nitrogen gas. The piston inside the cylinder moves up and down to create a compressible gas chamber. The key design elements include:
- Cylinder: Usually made of high-strength steel to withstand high pressures.
- Piston: A robust component that fits snugly inside the cylinder, ensuring minimal leakage and efficient gas compression.
- Sealing Mechanism: Advanced sealing technology prevents gas leakage, maintaining the pressure needed for optimal performance.
Construction:
- Materials: High-strength alloys are commonly used in construction to enhance durability and resistance to wear. The choice of materials ensures that the springs can operate efficiently under extreme conditions.
- Customization: Many manufacturers offer customized designs tailored to specific applications, allowing users to adjust the spring’s force output by changing the nitrogen pressure.
Die Springs
Design:
Die springs feature a simple yet effective design, consisting of coiled wire formed into various shapes, such as cylindrical, conical, or oval. The main design elements include:
- Spring Body: Typically made from high-carbon steel or stainless steel, providing resilience and the ability to withstand repeated cycles.
- Coil Configuration: Die springs can be designed in different coil configurations (e.g., round, square) to optimize load-bearing capabilities.
Construction:
- Materials: Die springs are often constructed from materials specifically selected for their fatigue resistance and strength, such as oil-tempered or chrome-silicon wire. These materials contribute to the springs’ longevity and performance in high-stress applications.
- Heat Treatment: Many die springs undergo heat treatment processes to enhance their mechanical properties, ensuring they maintain their shape and performance even after extensive use.
Performance Characteristics
Understanding the performance characteristics of Nitrogen Gas Springs for Dies vs Die Spring is crucial for selecting the right type of spring for your applications. Each spring type offers distinct advantages and functionalities tailored to different operational needs.
Nitrogen Gas Springs for Dies
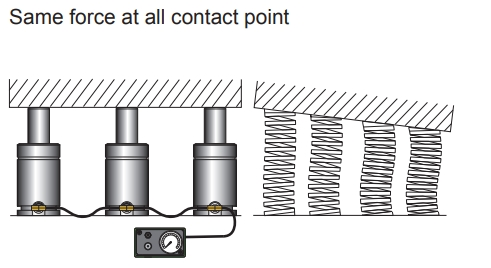
1. Load Capacity:
Nitrogen gas springs can deliver a high force output while maintaining a compact size. They are designed to handle loads ranging from a few hundred to several thousand pounds, depending on the model and nitrogen pressure.
2. Compression and Extension:
These springs provide smooth and controlled compression and extension. The gas within the spring allows for precise adjustments, enabling rapid actuation and responsiveness. This feature is especially valuable in applications requiring high-speed cycles and quick responses.
3. Damping Characteristics:
Nitrogen gas springs typically have excellent damping properties, which help reduce vibrations and noise during operation. This characteristic enhances the overall efficiency and performance of machinery utilizing these springs.
4. Consistency:
The performance of nitrogen gas springs remains consistent over time, even after extensive use. The sealed gas chamber minimizes the effects of wear and fatigue, ensuring reliable operation throughout the spring’s lifespan.
Die Springs
1. Load Capacity:
Die springs are designed to support heavy loads, making them suitable for high-stress applications. They can withstand a wide range of loads, with various spring rates available to accommodate specific requirements.
2. Compression and Extension:
While die springs also provide reliable compression and extension, their movement may not be as smooth or quick as that of nitrogen gas springs. The coil design can lead to a slower response time in certain applications.
3. Fatigue Resistance:
One of the standout features of die springs is their superior fatigue resistance. Engineered to endure repetitive cycles without significant degradation, they are an excellent choice for applications involving continuous movement and high cycle rates.
4. Stability:
Die springs maintain their shape and performance under heavy loads. This stability is crucial for applications in stamping and molding processes, where consistent force application is required.
Applications
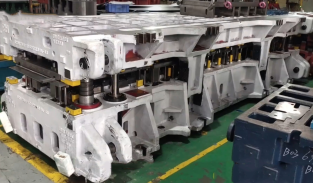
Nitrogen Gas Springs for Dies
- Molding and Die-Casting:
Nitrogen gas springs are commonly used in injection molding and die-casting processes. Their ability to provide rapid actuation and precise force control makes them ideal for ejecting molded parts efficiently. This speed is crucial for maintaining high production rates in manufacturing. - Stamping Operations:
In stamping applications, nitrogen gas springs are employed to facilitate quick and consistent motion. They help in the stamping of metal parts, providing the necessary force to ensure accurate and repeatable results. - Automotive Industry:
Nitrogen gas springs are widely used in the automotive sector for applications such as hood lifts, trunk supports, and other mechanisms requiring reliable force and motion. Their adjustable nature allows for customization based on vehicle design and weight specifications. - Aerospace and Defense:
In aerospace applications, nitrogen gas springs provide the needed reliability and performance in critical systems. They are used in landing gear mechanisms, cargo doors, and other areas where consistent and safe operation is paramount.
Die Springs
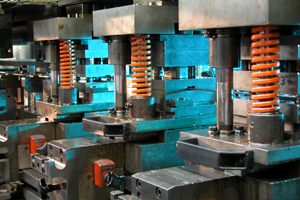
- Tooling and Die Applications:
Die springs are extensively used in tooling and die applications, where high load-bearing capacity and durability are essential. They provide consistent force in die assemblies, ensuring precision during the manufacturing process. - Injection Molding:
While nitrogen gas springs are often used in molding, die springs also play a significant role in injection molding machines. They support molds during clamping and ejection processes, contributing to overall efficiency and productivity. - Assembly Line Automation:
Die springs are utilized in assembly line automation for repetitive tasks that require high load support. Their fatigue resistance allows for reliable performance over extended periods, making them ideal for manufacturing environments. - Heavy Machinery:
In construction and heavy machinery, die springs are used to absorb shocks and maintain stability under significant loads. Their robust construction makes them suitable for applications that endure harsh conditions and continuous use.
Advantages
In summary, Nitrogen Gas Springs for Dies offer adjustable force and quick actuation, making them ideal for high-speed applications, while Die Springs excel in load capacity and durability, suitable for heavy-duty use. Understanding these advantages can aid in selecting the right spring for your specific needs.
Advantages of Nitrogen Gas Springs for Dies
1. Adjustable Force:
One of the primary benefits of nitrogen gas springs is their adjustable force output. By changing the nitrogen pressure, users can customize the spring’s performance to meet specific operational requirements, allowing for flexibility in various applications.
2. Quick Actuation:
Nitrogen gas springs provide rapid response times, making them ideal for high-speed applications. This quick actuation helps improve production efficiency, especially in processes that require fast cycles, such as molding and stamping.
3. Damping and Noise Reduction:
These springs offer excellent damping characteristics, helping to minimize vibrations and noise during operation. This feature enhances overall system performance and creates a more pleasant working environment.
4. Consistent Performance:
With a sealed gas chamber, nitrogen gas springs maintain consistent performance over time, even after extensive use. This reliability is crucial in applications where precision and safety are paramount.
Advantages of Die Springs
1. High Load Capacity:
Die springs are designed to support substantial loads, making them suitable for heavy-duty applications. Their robust construction allows them to withstand high stress and maintain their shape under pressure.
2. Durability and Longevity:
Die springs are engineered for durability and can endure numerous cycles without significant wear. Their fatigue resistance ensures that they perform reliably over long periods, making them a cost-effective choice for manufacturers.
3. Simplicity of Design:
The simple coil design of die springs makes them easy to install and maintain. Their straightforward construction allows for quick replacement and reduces downtime in manufacturing processes.
4. Versatile Applications:
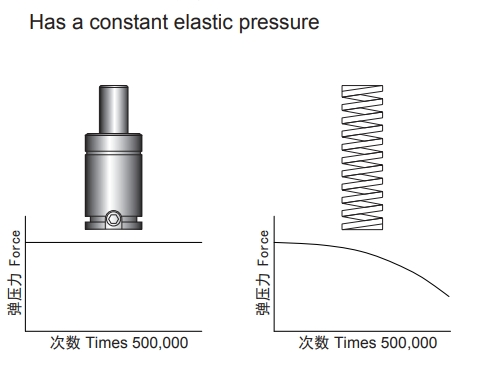
Die springs can be used in various applications across multiple industries, including tooling, automation, and heavy machinery. Their versatility makes them an essential component in many manufacturing settings.
Disadvantages
Disadvantages of Nitrogen Gas Springs for Dies
1. Initial Cost:
Nitrogen gas springs typically have a higher upfront cost compared to die springs. The advanced technology and materials used in their construction contribute to this higher price, which can be a consideration for budget-conscious projects.
2. Maintenance Requirements:
Although nitrogen gas springs are designed for longevity, they may require periodic maintenance to ensure proper performance. Users must monitor the gas pressure and seal integrity, which can add to operational complexity.
3. Sensitivity to Environmental Conditions:
Nitrogen gas springs can be sensitive to temperature variations. Extreme temperatures can affect gas pressure and performance, making them less suitable for environments with fluctuating conditions without additional protective measures.
4. Potential for Gas Leakage:
Although modern nitrogen gas springs are designed to minimize leakage, there is still a risk of gas escaping over time, which can lead to diminished performance. Regular checks are necessary to maintain their efficiency.
Disadvantages of Die Springs
1. Limited Force Adjustability:
Unlike nitrogen gas springs, die springs do not offer the same level of force adjustability. Users must select the appropriate spring based on fixed characteristics, which may limit flexibility in some applications.
2. Slower Response Time:
Die springs generally have a slower actuation response compared to nitrogen gas springs. This characteristic can be a disadvantage in high-speed applications where quick movement is essential.
3. Potential for Fatigue:
While die springs are designed for durability, they are still subject to fatigue over time. Repeated cycling under heavy loads can eventually lead to performance degradation, necessitating replacement sooner than expected in high-stress environments.
4. Bulkier Design:
Die springs often have a bulkier design compared to nitrogen gas springs, which can limit their use in compact spaces. This size difference can affect installation options in applications with space constraints.
Cost Comparison
When deciding between Nitrogen Gas Springs for Dies vs Die Spring, cost is an essential factor that can influence your choice. Understanding the price differences and the overall value each type of spring offers is crucial for making an informed decision.
Initial Purchase Cost
Nitrogen Gas Springs for Dies typically have a higher initial purchase cost than die springs. The advanced technology, materials, and manufacturing processes involved in producing nitrogen gas springs contribute to their elevated price. On average, nitrogen gas springs can cost anywhere from 20% to 50% more than standard die springs, depending on their specifications and features.
Die Springs, on the other hand, are generally more affordable due to their simpler design and construction. This makes them an attractive option for projects with tight budgets. However, the lower initial cost of die springs can sometimes lead to increased long-term expenses if they require frequent replacements or fail under heavy loads.
Long-term Cost Considerations
Nitrogen Gas Springs for Dies tend to have a higher upfront cost but may offer better long-term value due to their durability and reduced maintenance needs. Die Springs are more affordable initially but may incur higher replacement costs in demanding applications. Evaluating both the initial purchase price and the long-term expenses is vital for making the right choice for your specific needs.
1. Maintenance Costs:
While nitrogen gas springs may have higher initial costs, they can potentially save money in the long run due to their durability and lower maintenance requirements. Regular monitoring is necessary, but they often require less frequent replacement compared to die springs, which may need to be replaced more often in high-stress applications.
2. Replacement Frequency:
Die springs, although initially cheaper, may not provide the same lifespan as nitrogen gas springs in demanding environments. Frequent replacements can add up over time, leading to higher overall costs. If your application involves high cycle rates or heavy loads, the cost of replacing die springs may outweigh the savings from their lower initial price.
3. Operational Efficiency:
The performance characteristics of nitrogen gas springs—such as their quick actuation and damping properties—can lead to increased operational efficiency. This efficiency can translate to higher productivity and reduced cycle times, potentially offsetting their higher purchase price.
Installation and Maintenance
In conclusion, both Nitrogen Gas Springs for Dies and Die Springs require proper installation and maintenance practices to ensure optimal performance and longevity. Adhering to manufacturer guidelines and conducting regular inspections will help you maintain these vital components effectively.
Installation of Nitrogen Gas Springs for Dies
1. Preparation:
Before starting the installation, gather all necessary tools and equipment, such as wrenches, torque tools, and safety gear. Make sure the workspace is clean and free from any obstructions.
2. Check Specifications:
Refer to the manufacturer’s specifications for the correct model and size of the nitrogen gas spring to ensure compatibility with your application. This step is crucial to avoid performance issues later on.
3. Mounting Orientation:
Nitrogen gas springs can be installed in various orientations (horizontal, vertical, or angled), but it’s important to follow the manufacturer’s guidelines. Correct orientation helps maintain optimal performance and prevents premature wear.
4. Secure the Spring:
Attach the nitrogen gas spring to its designated mounting points using appropriate fasteners. Ensure that the spring is securely mounted and that there is no movement during operation.
5. Pressure Adjustment:
After installation, check the nitrogen pressure within the spring. If adjustments are needed, follow the manufacturer’s instructions to safely increase or decrease the pressure according to the application requirements.
Maintenance of Nitrogen Gas Springs for Dies
1. Regular Inspections:
Conduct regular inspections to check for signs of gas leakage, wear, or damage to seals. Early detection of issues can prevent more significant problems down the line.
2. Pressure Monitoring:
It’s essential to monitor the nitrogen pressure regularly. Ensure the pressure remains within the specified range, and recharge the spring if the pressure drops.
3. Lubrication:
While nitrogen gas springs are low-maintenance, applying lubricant to the moving parts can reduce friction and prolong their life. Use the recommended lubricants as specified by the manufacturer.
Installation of Die Springs
1. Simple Installation Process:
Die springs are generally easier to install due to their straightforward design. Begin by ensuring the installation area is clean.
2. Positioning the Springs:
Place the die springs in their designated locations. Make sure they are correctly oriented to function effectively during operation.
3. Securing the Springs:
Use appropriate fasteners to secure the die springs in place, ensuring they are tightly fastened to prevent movement.
Maintenance of Die Springs
1. Periodic Inspections:
Regularly inspect die springs for signs of wear, fatigue, or damage. Look for any cracks, deformations, or discoloration.
2. Cleaning:
Keep die springs clean and free of debris. Dirt and grime can hinder their performance, so a regular cleaning schedule is advisable.
3. Replacement Planning:
Plan for regular replacements based on usage frequency and load conditions. This proactive approach can help prevent unexpected failures.
Longevity and Durability
when comparing Nitrogen Gas Springs for Dies vs Die Spring, nitrogen gas springs generally offer superior longevity and durability. Their ability to withstand high cycles, resist environmental factors, and maintain consistent performance makes them a preferred choice for demanding applications. On the other hand, die springs can still be effective for less demanding tasks but may require more frequent maintenance and replacements.
Longevity of Nitrogen Gas Springs for Dies
1. Enhanced Lifespan:
Nitrogen gas springs are designed for high-performance applications and generally offer a longer lifespan compared to traditional die springs. Their sealed design minimizes wear and tear, allowing them to withstand higher cycles without significant degradation.
2. Gas Pressure Maintenance:
The internal nitrogen gas helps maintain consistent pressure, which reduces the likelihood of fatigue failure over time. This means that nitrogen gas springs can continue to perform effectively even under demanding conditions.
3. Resistance to Environmental Factors:
Many nitrogen gas springs are constructed with materials that resist corrosion and other environmental factors. This durability extends their operational life, making them suitable for various industrial applications where conditions may vary.
Longevity of Die Springs
1. Standard Lifespan:
Die springs typically have a shorter lifespan than nitrogen gas springs due to their simpler construction. While they are reliable for many applications, they may not hold up as well under continuous heavy loads or high cycle rates.
2. Wear and Fatigue:
Die springs are prone to wear and fatigue over time, especially in applications that involve frequent compressions and extensions. This can lead to decreased performance and, eventually, the need for replacement.
3. Environmental Sensitivity:
Die springs can be affected by environmental conditions such as moisture and temperature variations. While some die springs are treated for corrosion resistance, they may not perform as well as nitrogen gas springs in harsh environments.
Comparing Durability
1. Load Capacity:
Nitrogen gas springs are designed to handle heavier loads with minimal deflection, making them ideal for high-stress applications. In contrast, while die springs can also manage significant loads, their performance may degrade faster under similar conditions.
2. Maintenance Requirements:
The durability of nitrogen gas springs often translates to lower maintenance requirements. Users can expect less frequent replacements and repairs compared to die springs, which may require more regular attention to maintain optimal function.
Safety Considerations
Nitrogen Gas Springs for Dies and Die Springs require careful attention to safety considerations. Understanding the potential hazards, following manufacturer guidelines, and implementing proper training protocols will help ensure a safe working environment.
Safety Considerations for Nitrogen Gas Springs for Dies
1. Pressure Hazards:
Nitrogen gas springs operate under high pressure, which poses risks if they are improperly handled or maintained. Always follow the manufacturer’s guidelines for pressure settings and adjustments. Ensure that pressure relief procedures are in place to avoid accidents during maintenance.
2. Proper Installation:
Correct installation is crucial for safety. Ensure that the nitrogen gas spring is securely mounted to prevent it from dislodging during operation. Always use the recommended fasteners and check connections to ensure they can withstand operational forces.
3. Handling Procedures:
When transporting or handling nitrogen gas springs, wear appropriate personal protective equipment (PPE) such as gloves and safety goggles. Be aware of the weight and size of the springs to avoid injury during handling.
4. Training and Awareness:
Ensure that all personnel involved in the installation, operation, and maintenance of nitrogen gas springs receive adequate training. Familiarity with the risks and proper handling techniques will help reduce the likelihood of accidents.
Conclusion
choosing between Nitrogen Gas Springs for Dies and Die Springs involves weighing the pros and cons of each. For applications requiring high performance and durability, nitrogen gas springs are often the preferred choice. However, for simpler, less demanding tasks, die springs may still be an adequate solution.
Key Takeaways
- Functionality: Nitrogen gas springs provide superior functionality in high-performance applications, offering consistent pressure and minimal wear. In contrast, die springs are more traditional and may be suitable for less demanding tasks.
- Design and Durability: Nitrogen gas springs are built for longevity and durability, often outlasting die springs and reducing the need for frequent replacements. This longevity translates to less environmental waste.
- Performance and Applications: While nitrogen gas springs excel in high-stress environments, die springs can still effectively serve various industrial applications. The choice should be based on the specific needs of your projects.
- Safety and Maintenance: Both spring types require careful attention to safety and maintenance procedures. Proper handling and regular inspections are essential for ensuring their safe operation.
- Environmental Impact: Nitrogen gas springs generally have a lower environmental impact due to their longer lifespan and better recycling potential compared to die springs, which can contribute to more material waste.
Are you ready to enhance your manufacturing processes with the right spring solutions? Whether you are considering Nitrogen Gas Springs for Dies or traditional Die Springs, we are here to help you make an informed decision.
- Explore Our Products: Visit our website to learn more about our range of nitrogen gas springs and die springs designed to meet your specific needs.
- Request a Quote: Contact us today for a personalized quote and discover how our products can improve your operations.
- Subscribe for Updates: Stay updated with the latest trends, tips, and innovations in the spring industry by subscribing to our newsletter.
- Ask an Expert: Have questions or need assistance? Don’t hesitate to reach out! Our team of experts is ready to provide you with the guidance you need.