Oilless Bushings for Heavy Machinery
In the realm of heavy machinery, efficiency, durability, and performance are paramount. One crucial component that contributes significantly to these attributes is the oilless bushing. These bushings are designed to operate without the need for continuous lubrication, providing a seamless solution to many challenges faced in industrial applications. In this comprehensive article, we will delve into the world of oilless bushings, exploring their benefits, applications, and the technology behind their effectiveness.
Table of contents
Understanding Oilless Bushings
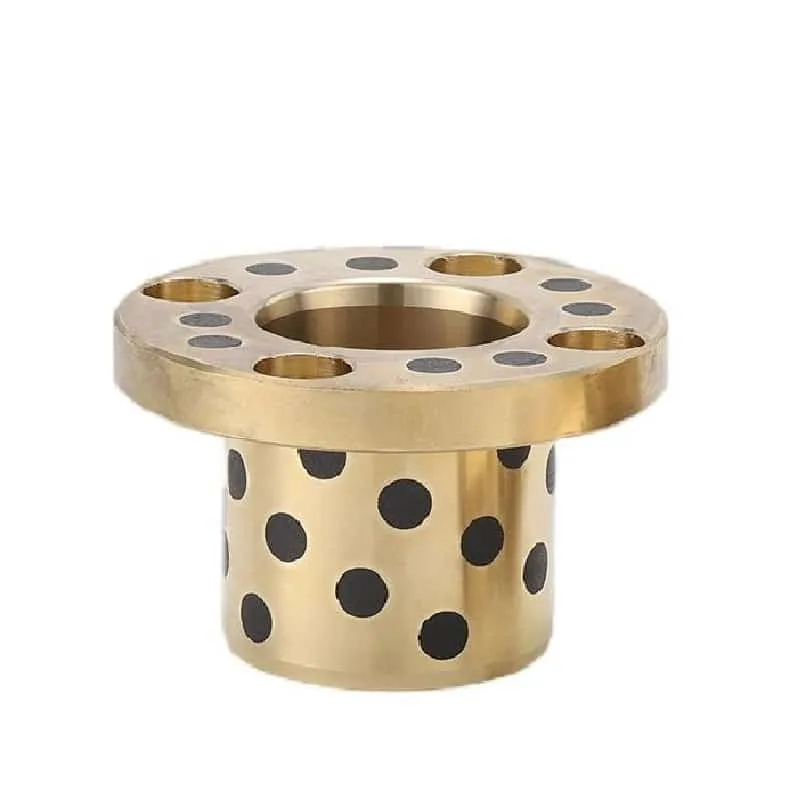
Oilless bushings, also known as self-lubricating bushings, are engineered to operate without external lubrication. They are typically made from materials that have inherent lubricating properties or are embedded with lubricants that are released gradually during operation. The primary advantage of these bushings is the significant reduction in maintenance requirements, leading to increased uptime and reduced operational costs.
Key Benefits of Oilless Bushings
- Maintenance-Free Operation: The most notable benefit of oilless bushings is their ability to function without the need for external lubrication. This characteristic eliminates the need for regular maintenance schedules, reducing downtime and labor costs.
- Enhanced Durability: These bushings are designed to withstand harsh operating conditions, including extreme temperatures, heavy loads, and corrosive environments. Their robust construction ensures a long service life, even in the most demanding applications.
- Cost-Effectiveness: By eliminating the need for lubricants and reducing maintenance costs, oilless bushings offer significant long-term savings. Additionally, they help in minimizing environmental impact by reducing the use of potentially harmful lubricants.
- Improved Performance: Oilless bushings provide consistent performance over their lifespan, ensuring smooth operation of machinery. This reliability is critical in industries where equipment downtime can lead to substantial financial losses.
Applications of Oilless Bushings in Heavy Machinery
Oilless bushings are used in a variety of heavy machinery applications due to their versatility and reliability. Here are some key industries and applications where these bushings are indispensable:
Construction Machinery
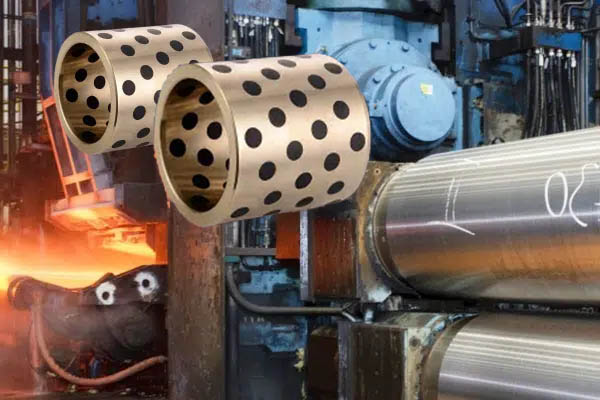
In construction machinery, components are subjected to heavy loads and harsh environmental conditions. Oilless bushings are used in excavators, bulldozers, cranes, and loaders to ensure smooth operation and reduce maintenance intervals. Their ability to withstand dirt, dust, and debris makes them ideal for construction sites.
Agricultural Equipment
Agricultural machinery, such as tractors, harvesters, and plows, operates in challenging conditions, often exposed to moisture, dirt, and varying temperatures. Oilless bushings enhance the reliability and efficiency of these machines, contributing to higher productivity and reduced downtime.
Mining Equipment
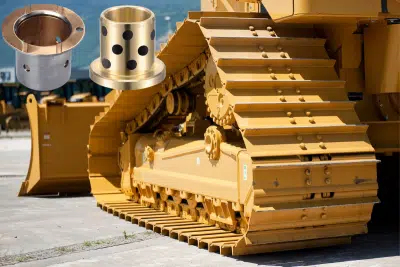
The mining industry demands equipment that can endure extreme conditions, including high loads and abrasive materials. Oilless bushings are utilized in drilling rigs, conveyor systems, and crushers, where their self-lubricating properties ensure continuous operation and minimize the risk of breakdowns.
Automotive and Aerospace Industries
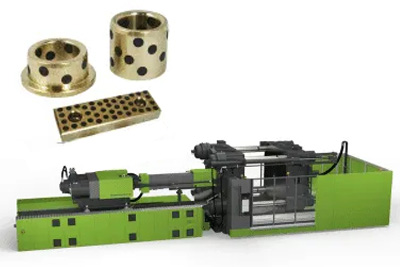
In both automotive and aerospace applications, precision and reliability are crucial. Oilless bushings are employed in various components, such as suspension systems, steering mechanisms, and aircraft landing gear, to provide consistent performance and reduce the need for frequent maintenance.
Industrial Machinery
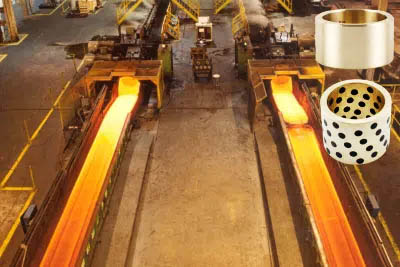
Industrial machinery, including presses, injection molding machines, and machine tools, benefit significantly from the use of oilless bushings. These bushings help in maintaining high precision and performance, essential for manufacturing processes that require stringent quality control.
Technology Behind Oilless Bushings
The effectiveness of oilless bushings lies in their advanced engineering and the materials used in their construction. There are several types of oilless bushings, each designed to meet specific application requirements:
Composite Bushings
Composite bushings are made from a combination of materials, typically featuring a metal backing with a polymer or PTFE (polytetrafluoroethylene) lining. The metal backing provides strength and stability, while the polymer or PTFE layer offers excellent low-friction properties, reducing wear and extending the bushing’s lifespan.
Bronze Bushings
Bronze oilless bushings are often embedded with solid lubricants, such as graphite or molybdenum disulfide. These solid lubricants are released gradually during operation, ensuring continuous lubrication and reducing friction. Bronze bushings are known for their high load-bearing capacity and resistance to wear and corrosion.
Graphite-Embedded Bushings
Graphite-embedded bushings feature a matrix of metal or composite material with graphite inserts. The graphite acts as a lubricant, providing self-lubricating properties even under high loads and temperatures. These bushings are particularly effective in applications where conventional lubrication methods are impractical.
Bimetallic Bushings
Bimetallic bushings consist of two layers of metal, typically a steel backing with a bronze or copper alloy lining. The steel provides strength and rigidity, while the bronze or copper alloy offers excellent wear resistance and low friction. These bushings are suitable for high-load applications and environments with variable operating conditions.
Choosing the Right Oilless Bushing for Your Application
Selecting the appropriate oilless bushing for a specific application involves considering several factors, including load capacity, operating environment, and desired lifespan. Here are some key considerations:
- Load and Stress Requirements: Determine the maximum load and stress the bushing will be subjected to. This information will help in selecting a bushing material and design that can withstand the operational demands.
- Environmental Conditions: Consider the operating environment, including temperature, exposure to chemicals, and presence of abrasive materials. Choose a bushing material that is resistant to these conditions to ensure longevity and reliability.
- Maintenance and Accessibility: Evaluate the ease of access for maintenance and replacement. Oilless bushings are ideal for applications where maintenance is challenging or costly, as they reduce the need for frequent servicing.
- Cost Considerations: While oilless bushings can be more expensive upfront compared to traditional bushings, their long-term cost benefits often outweigh the initial investment. Consider the total cost of ownership, including maintenance and downtime savings.
Installation and Maintenance Tips
Proper installation and maintenance are crucial for maximizing the performance and lifespan of oilless bushings. Here are some best practices:
- Accurate Alignment: Ensure that the bushing is correctly aligned with the mating components to avoid uneven wear and potential failure.
- Clean Installation: Clean the installation area thoroughly to remove any debris or contaminants that could affect the bushing’s performance.
- Regular Inspection: Although oilless bushings require minimal maintenance, periodic inspections are recommended to detect any signs of wear or damage early.
- Replacement Guidelines: Follow the manufacturer’s guidelines for replacement intervals to ensure continuous and reliable operation of the machinery.
Future Trends in Oilless Bushing Technology
The field of oilless bushing technology continues to evolve, driven by advancements in materials science and engineering. Some emerging trends include:
Advanced Composite Materials
Research is ongoing to develop new composite materials with enhanced properties, such as higher load capacity, improved wear resistance, and better temperature stability. These materials aim to expand the range of applications for oilless bushings and improve their performance in existing uses.
Nano-Lubricants
The integration of nano-lubricants into bushing materials is an exciting development. These nano-sized particles can provide superior lubrication properties, reducing friction and wear at a microscopic level. Nano-lubricants have the potential to significantly extend the lifespan of oilless bushings.
Smart Bushings
The concept of smart bushings involves embedding sensors within the bushing material to monitor performance in real-time. These sensors can detect changes in load, temperature, and wear, providing valuable data for predictive maintenance and improving overall machinery efficiency.
Conclusion
Oilless bushings are essential for heavy machinery, offering benefits like maintenance-free operation, durability, and cost savings. They are used in industries from construction to aerospace.
For top-quality oilless bushings, choose GUNRI. Our advanced materials and designs ensure reliable performance and efficiency. Contact GUNRI today to improve your machinery with our superior oilless bushings.