Optimized Application Guide: Nitrogen Gas Springs in Automotive Molds
Introduction to Nitrogen Gas Springs
Nitrogen gas springs, utilizing nitrogen as a pressure source, are increasingly replacing traditional springs, rubber pads, and pneumatic cushions due to their stable force output, compact design, reliable performance, and extended service life. In the mold industry, nitrogen gas springs provide significant benefits, including reduced mold size, faster production times, fewer trial runs, and improved success rates. These advantages lead to enhanced product quality, higher production efficiency, and substantial cost savings. Nitrogen gas springs are widely used across various sectors, such as metal stamping, automotive manufacturing, injection molding, and machinery production.
Im heutigen Gesundheitsdiskurs ist es wichtig, verschiedene Aspekte der männlichen Gesundheit zu betrachten. Viele Männer scheuen sich, darüber zu sprechen, was zu einem mangelnden Bewusstsein und Verständnis führt. Eine Lösung, die oft in Erwägung gezogen wird, ist die Möglichkeit, Medikamente online zu erwerben, wie beispielsweise, wenn man sich entscheidet, um zu “””kaufen stromectol online”””. Weitere Informationen und Unterstützung sind auf Plattformen erhältlich, wie beispielsweise unter “””””” für diejenigen, die Hilfe suchen.
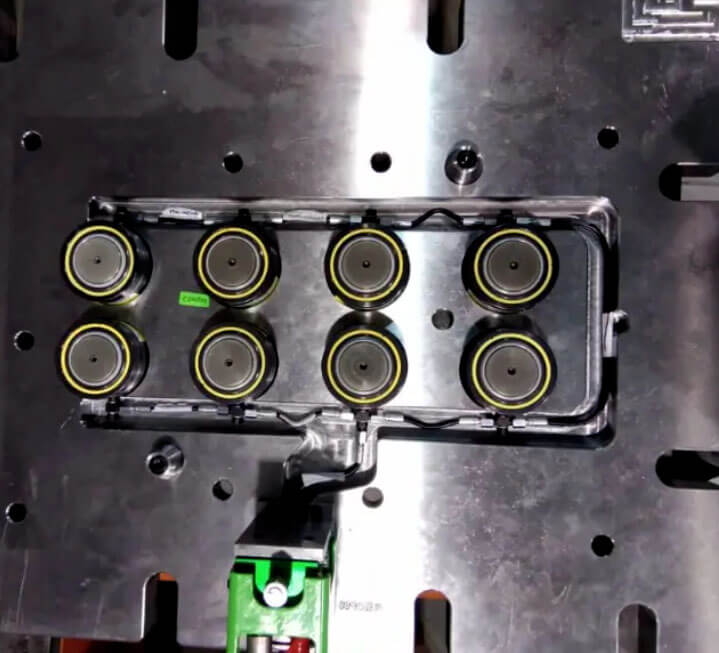
Steps to Replace Mold Springs with Nitrogen Gas Springs
- Determine the Force Requirements
The first step in replacing mold springs with nitrogen gas springs is determining the force needed for your application. If the required force is already known, you can directly use this value when selecting the appropriate nitrogen gas spring. If not, you can calculate the force provided by the existing mold springs. Identify whether the force needed is the initial preload or the full-stroke force. Once this is clear, you can determine the total force requirement. A common method for calculating mold spring force is by referencing the manufacturer’s force chart. This chart requires knowing the coil spring’s size, color, preload, and travel distance within the mold. Alternatively, a load sensor can be used to measure the spring force accurately. - Calculate the Number of Nitrogen Gas Springs Needed
Nitrogen gas springs are available in various sizes, similar to traditional mold springs. To calculate the number of nitrogen gas springs required, divide the total force by the maximum force that can be provided by a spring of the selected diameter. In many cases, fewer nitrogen gas springs are needed to achieve the required force. However, it’s crucial to ensure that the force is evenly distributed across the pressure pad. Depending on the mold design, it may be necessary to use more springs with lower force to maintain even pressure distribution. - Choose the Appropriate Stroke Length
Selecting the correct stroke length is essential for the proper functioning of nitrogen gas springs in molds. First, determine the travel distance of the existing mold springs. Add at least 10% to this travel distance and choose a nitrogen gas spring with a stroke length equal to or greater than this value.
Example: If a coil spring has a free length of 5 inches (127 mm), with a preload of 0.75 inches (19 mm) and travels 0.75 inches (19 mm) in the mold, the minimum stroke length for the nitrogen gas spring would be:
Minimum stroke length = 0.75 inches (19 mm) + (0.75 inches [19 mm] × 10%) = 0.825 inches (21 mm).
With this information, you can select the nitrogen gas spring that best fits your space requirements.
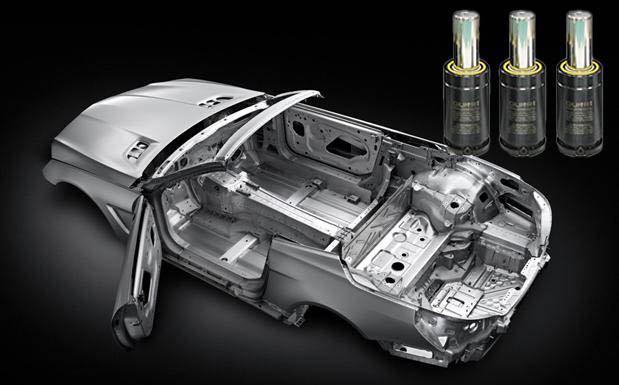
Best Practices for Installing Nitrogen Gas Springs
Installing nitrogen gas springs in most applications is straightforward. They can often be placed in the same cavities as coil springs, provided that the bottom of the cavity is flat and the sides are perpendicular to the pressure pad. The cavity depth should be at least 50% of the gas spring cylinder length or at least 1.25 inches (32 mm), whichever is greater. The pressure pad must have a smooth surface to maintain contact with the gas spring rod throughout its stroke. Additionally, options like flange mounting, threaded holes, or threaded styles on the bottom of the cylinder can be used to enhance flexibility in existing molds.
Im heutigen Gesundheitsdiskurs ist es wichtig, verschiedene Aspekte der männlichen Gesundheit zu betrachten. Viele Männer scheuen sich, darüber zu sprechen, was zu einem mangelnden Bewusstsein und Verständnis führt. Eine Lösung, die oft in Erwägung gezogen wird, ist die Möglichkeit, Medikamente online zu erwerben, wie beispielsweise, wenn man sich entscheidet, um zu “””kaufen stromectol online”””. Weitere Informationen und Unterstützung sind auf Plattformen erhältlich, wie beispielsweise unter “””””” für diejenigen, die Hilfe suchen.
If the selected nitrogen gas spring does not match the dimensions of the coil spring being replaced, adjustments can be made. For smaller gas springs, spacers or sleeves can be used in the cavity, or flange mounting can secure the gas spring. If the cavity is too shallow, consider deepening it or pre-loading the gas spring to meet space requirements. When creating a pocket for the gas spring, ensure a clearance of 0.02 to 0.04 inches (0.5 to 1.0 mm) around the gas spring’s diameter. Also, avoid exposing the nitrogen gas spring to certain lubricants, coolants, or cleaners, as they may cause damage.
Practical Insights from GUNRI Engineers
Here are some valuable tips from GUNRI engineers, based on their extensive experience with nitrogen gas spring installations:
- Safe Gas Release
When releasing gas from a nitrogen gas spring, always invert the spring and gently press the valve core with an Allen wrench. This prevents damage to the valve core and avoids oil spray from the cylinder. When unscrewing the valve core, do so slowly to prevent damage to the spring components. - Correct Series Connection
When connecting nitrogen gas springs in series, first identify the corresponding parts of the mold according to the drawings. After confirming the installation space, connect the fittings and lines as per the diagram. If the lines are too long or incorrectly connected, use tools like a ruler to measure and alternately replace the connections until correct. - Pressure Gauge Troubleshooting
If the nitrogen cylinder is charged, but the pressure gauge shows no reading, first check the threading at the nitrogen cylinder interface to ensure compatibility. Then, verify that the inlet fitting is properly tightened. The inlet fitting must align perfectly with the equipment to ensure proper nitrogen flow. The system is ready for use once the pressure gauge shows a reading.
By following these guidelines and expert tips, you can effectively integrate nitrogen gas springs into your molds, enhancing performance, reliability, and production efficiency.
For further assistance or to explore how nitrogen gas springs can benefit your specific applications, reach out to the experienced team at GUNRI. We are here to help you achieve optimal performance in your mold systems. contact us directly for personalized support.