Optimizing Nitrogen Gas Spring Installation in Stamping Dies
In the realm of industrial manufacturing, precision and efficiency are paramount. Nowhere is this more evident than in the intricate processes of stamping dies. Among the various components employed in these processes, nitrogen gas springs play a crucial role in ensuring smooth operations and prolonged tool life. However, the installation of these nitrogen gas springs warrants careful consideration, especially concerning flange integration, to optimize performance and longevity.
The Significance of Nitrogen Gas Springs
Before delving into the nuances of installation, it’s essential to grasp the importance of nitrogen gas springs within stamping dies. These springs are instrumental in counteracting the forces exerted during the stamping process. By utilizing compressed nitrogen gas, they provide consistent and controllable pressure, facilitating precise movements and reducing wear on the die components.
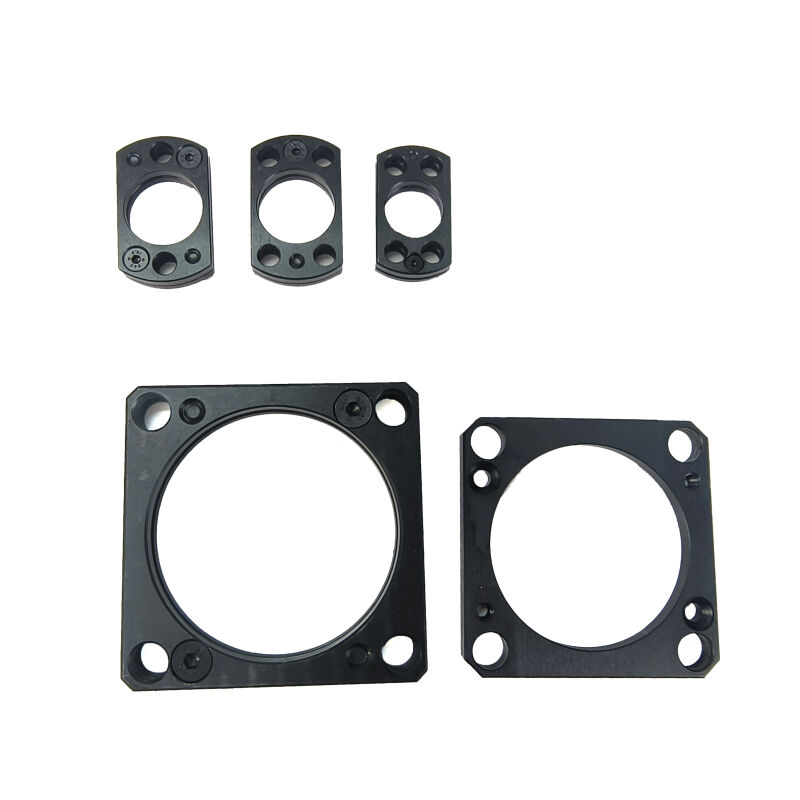
Installation Challenges
While the benefits of nitrogen gas springs are clear, their optimal integration within stamping dies presents challenges, particularly regarding installation methods. In scenarios involving small pressure and stroke requirements, conventional installation involves securing the gas spring within the mold using countersunk holes. This method ensures stability during operation, preventing undesirable displacements that could compromise the integrity of the stamping process.
Adapting to Varied Demands
However, the landscape shifts when confronted with larger forces, extended strokes, or directional stamping force prerequisites. In such cases, a more robust approach is warranted, necessitating the utilization of flanges to complement the nitrogen gas springs. These flanges serve as critical components that facilitate secure and reliable mounting within the mold. By distributing forces evenly and enhancing stability, flanges elevate the performance of nitrogen gas springs, enabling them to withstand demanding operational conditions.
The Role of Flanges in Optimization
The integration of flanges represents a paradigm shift in nitrogen gas spring installation, offering a host of benefits that extend beyond mere structural support. Firstly, flanges mitigate the risk of lateral forces being exerted on the gas spring, thereby safeguarding its operational integrity and longevity. Additionally, they enhance rigidity, reducing the likelihood of premature wear and tear caused by excessive vibrations or movements within the die.
Ensuring Longevity and Efficiency
By prioritizing the proper installation of nitrogen gas springs with flanges, manufacturers can unlock a multitude of advantages. Enhanced stability and reliability translate into improved product quality, as dimensional accuracy and consistency are maintained throughout the stamping process. Moreover, the longevity of both the nitrogen gas springs and the stamping dies themselves is prolonged, leading to reduced downtime and maintenance costs over the lifespan of the equipment.
Conclusion
In the intricate dance of industrial manufacturing, every component plays a vital role in ensuring seamless operations and superior outcomes. Nitrogen gas springs, with their ability to provide precise and consistent force, are indispensable assets within stamping dies. However, their efficacy is contingent upon meticulous installation, particularly when confronted with challenging operational parameters. By embracing flanges as integral components of the installation process, manufacturers can optimize the performance and longevity of nitrogen gas springs, thereby elevating the efficiency and reliability of their stamping operations.