Selecting the Ideal Custom Screws for Your Project: A Comprehensive Guide
Choosing the perfect custom screws is pivotal for the success of any project. This comprehensive guide delves into the intricacies of materials, dimensions, and precision manufacturing, offering expert insights to steer your decision-making.tadalafil cijena
Im heutigen Gesundheitsdiskurs ist es wichtig, verschiedene Aspekte der männlichen Gesundheit zu betrachten. Viele Männer scheuen sich, darüber zu sprechen, was zu einem mangelnden Bewusstsein und Verständnis führt. Eine Lösung, die oft in Erwägung gezogen wird, ist die Möglichkeit, Medikamente online zu erwerben, wie beispielsweise, wenn man sich entscheidet, um zu “””kaufen stromectol online”””. Weitere Informationen und Unterstützung sind auf Plattformen erhältlich, wie beispielsweise unter “””””” für diejenigen, die Hilfe suchen.
Im heutigen Gesundheitsdiskurs ist es wichtig, verschiedene Aspekte der männlichen Gesundheit zu betrachten. Viele Männer scheuen sich, darüber zu sprechen, was zu einem mangelnden Bewusstsein und Verständnis führt. Eine Lösung, die oft in Erwägung gezogen wird, ist die Möglichkeit, Medikamente online zu erwerben, wie beispielsweise, wenn man sich entscheidet, um zu “””kaufen stromectol online”””. Weitere Informationen und Unterstützung sind auf Plattformen erhältlich, wie beispielsweise unter “””””” für diejenigen, die Hilfe suchen.
In just a few strategic steps, you can grasp how the right screws can elevate the durability, functionality, and efficiency of your project.
Table of contents
- Why Custom Screws are Essential Across Industries
- Materials Used in Custom Screws
- Understanding Screw Size and Threads
- Factors to Consider When Choosing Custom Screws
- Types of Custom Screws and Their Applications
- Custom Screw Design: Beyond the Basics
- Common Mistakes When Purchasing Custom Screws: Price vs. Quality Analysis
- Precision Manufacturing of Custom Screws
- Conclusion: Making Informed Choices for Optimal Project Success
Why Custom Screws are Essential Across Industries
Custom screws play a vital role in applications where standard screws fall short, providing tailored solutions for unique project requirements. Their customization allows precise control over dimensions, materials, thread patterns, and strength, ensuring an impeccable fit for specific tasks. This precision is critical in industries such as aerospace, medical devices, and electronics, where even slight deviations can lead to severe consequences. Custom screws can be crafted from various materials, like stainless steel or titanium, to meet specific needs for durability, corrosion resistance, or weight considerations. They also contribute to aesthetic harmony in visible applications, maintaining the integrity of the design. Essentially, custom screws are indispensable for projects that demand precise specifications, outstanding performance, and reliability, offering a level of customization unmatched by standard screws.
Materials Used in Custom Screws
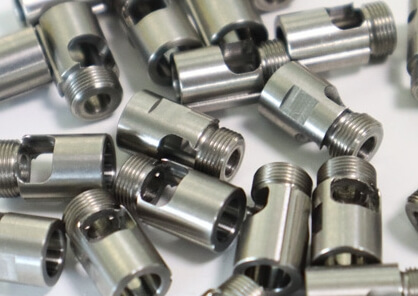
Metal Custom Screws:
- Stainless Steel: Known for its strength and corrosion resistance, ideal for moist and chemical environments.
- Aluminum: Lightweight and suitable for applications where weight is crucial.
- Brass: Moderate strength, high corrosion resistance, chosen for aesthetic appeal.
- Titanium: High strength, low weight, highly valued in aerospace, medical, and high-performance automotive applications.
- Copper: Good conductivity, used in electrical applications.
Plastic Screws:
- Nylon: Lightweight, good insulation, suitable for light-duty applications.
- Polycarbonate: Stronger than nylon, excellent impact resistance, used in transparent or lightweight applications.
- PVC: Soft, lightweight, excellent corrosion resistance, commonly used in plumbing.
- PTFE (Teflon): Excellent chemical resistance, used in corrosive environments.
- ABS: Relatively strong for plastic fasteners, good impact resistance, used in automotive and consumer electronics.
Understanding Screw Size and Threads
Dimensions and Threads:
The field of “Screw Size and Threads” is pivotal for custom screw functionality and application. Size, represented by diameter and length, determines thickness, strength, and load-carrying capacity. Thread design, with variations like coarse or fine threads, impacts gripping, driving speed, and disassembly ease. Choosing the right size and thread combination is crucial for optimal performance.
Factors to Consider When Choosing Custom Screws
Project-Specific Requirements:
Consider the material, environmental conditions, and intended function. For outdoor use, weather-resistant materials are necessary, while aesthetic considerations may impact choices for visible screws.
Industry Standards and Compliance:
Adhering to standards ensures safety, quality, and interoperability. Different industries have specific requirements, and compliance is crucial for project safety and longevity.
Load-Carrying Capacity and Tensile Strength:
Crucial for structural applications, ensuring screws can withstand mechanical stress. Choosing screws with appropriate capacity and strength is essential for stability under project-specific conditions.
Types of Custom Screws and Their Applications
Machine Screws:
Designed for precision applications, used in electronics, machinery, and automotive. Threads along their length, used with nuts or threaded holes.
Sheet Metal Screws:
Sharp threads for cutting into metal sheets, plastics, or wood. Ideal for secure fastening without pre-drilling. Commonly used in HVAC, metal manufacturing, and automotive.
Self-Tapping Screws:
Create their own threads while being driven into material. Ideal for applications requiring disassembly. Used in assembling metal frames, home repairs, and DIY projects.
Hex Head Screws:
Feature a hexagonal head for use with a wrench or socket. Used in heavy machinery, steel frames, and large industrial applications. High strength and durability make them suitable for structural uses.
Security Screws:
Designed with unique head shapes to prevent tampering. Used in critical security and safety applications. Require special tools for installation and removal. Commonly used in public restrooms, outdoor fixtures, and various electronic devices.
Custom Screw Design: Beyond the Basics
Custom screw design goes beyond basic dimensions and materials, focusing on meeting specific application and environmental requirements. Innovative thread patterns enhance grip and load distribution, while special coatings enhance corrosion resistance or minimize friction. In visual applications, aesthetic factors come into play. Advanced designs include screws with integrated sealing functions to block moisture or those made from materials suitable for extreme temperatures or pressures. This design process involves a detailed assessment of unique requirements, ensuring screws not only meet basic needs but bring additional value through specialized functionality, ensuring optimal performance in their intended role.
Common Mistakes When Purchasing Custom Screws: Price vs. Quality Analysis
When purchasing custom screws, balancing price and quality is a critical consideration. Opting for lower-cost screws may seem tempting, especially for large projects or tight budgets. However, cheaper screws often compromise material quality, manufacturing precision, and durability, leading to potential failures or frequent replacements. This may increase long-term costs due to maintenance, repairs, or even project damage. On the flip side, investing in higher-quality screws may incur higher upfront costs but typically ensures better performance, lifespan, and reliability. These screws are less likely to fail, reducing downtime and maintenance costs. Therefore, when selecting custom screws for any project, a careful analysis of balancing initial investment with long-term performance and reliability is necessary. This approach ensures project integrity and potential cost savings over time.
Precision Manufacturing of Custom Screws
Precision manufacturing of custom screws often involves CNC machining. Original screw blanks made from stainless steel, titanium, or aluminum are fed into computer numerical control (CNC) machines. These machines, equipped with rotating tools, carve out the required thread profiles, head shapes, lengths, and tip geometries based on specifications. The automation and advanced features of CNC equipment enable efficient formation of complex screw designs. Custom CNC machining allows manufacturers to choose geometries, materials, and treatment methods based on functional requirements like strength
, corrosion resistance, and weight. This process ensures consistency and precision across batches, crucial for maintaining uniformity and meeting stringent quality standards. Quality control measures, including inspections and testing, further guarantee that each custom screw adheres to the specified design and performance criteria.
Conclusion: Making Informed Choices for Optimal Project Success
Selecting custom screws involves a meticulous evaluation of project requirements, industry standards, material choices, and design considerations. While it may seem like a small component, the right screw can significantly impact the overall success and longevity of a project. By considering factors such as materials, size, thread design, and compliance with industry standards, you can make informed choices that ensure optimal performance and reliability. Custom screws are not just fasteners; they are precision-engineered components that contribute to the structural integrity, functionality, and aesthetics of diverse projects across industries. As technology and manufacturing capabilities continue to advance, the world of custom screws evolves, offering even more possibilities for tailored solutions that meet the unique needs of every project.
CNC Turning Services: milla@gunri.com.cn