Stamping Die Essentials: Deep Drawing
Deep drawing is a critical metal-forming process widely used in industries such as automotive, aerospace, and consumer goods manufacturing. It involves transforming flat sheet metal into complex three-dimensional shapes using a stamping die. This article explores the fundamentals of deep drawing, key components of stamping dies (including advanced elements like nitrogen springs and draw punch posts), and best practices to achieve optimal results.
What is Deep Drawing?
Deep drawing is a sheet metal forming process where a punch forces a metal blank into a die cavity, creating a hollow part with a depth greater than its diameter. Common applications include automotive fuel tanks, kitchen sinks, and battery casings. The process requires precise control of material flow, friction, and pressure to avoid defects like wrinkling, tearing, or uneven wall thickness.
Key Components of a Deep Drawing Die
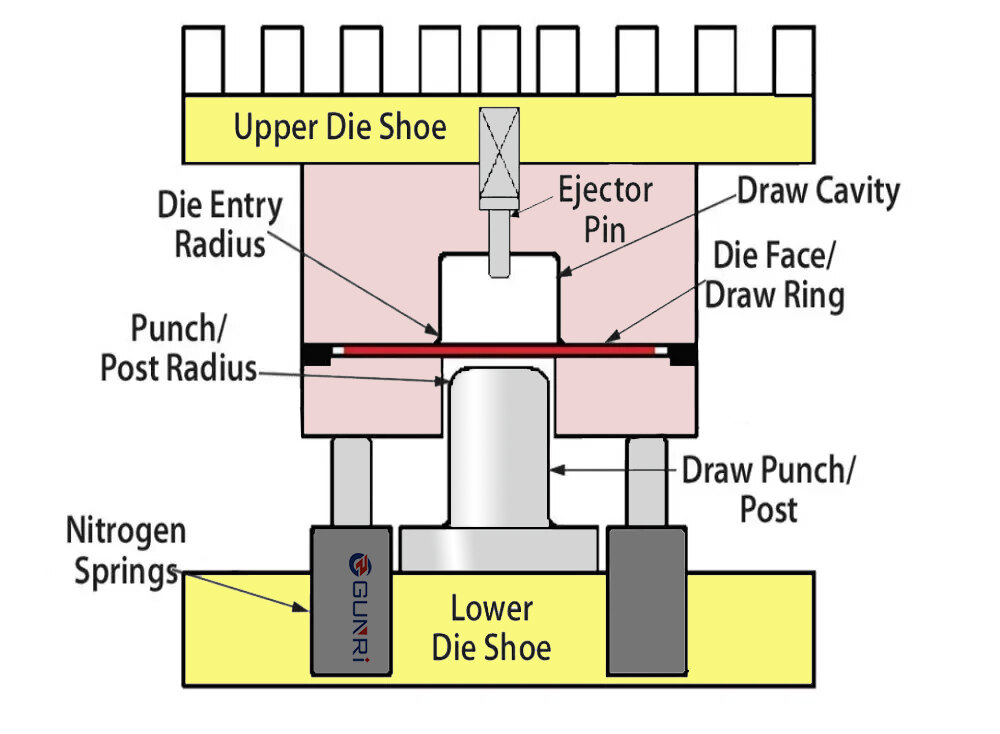
A deep drawing die system consists of several essential components:
- Punch: The tool that applies force to the metal blank, shaping it into the die cavity.
- Die Cavity: The hollow space that defines the final shape of the part.
- Blank Holder (Binder): Applies pressure to the edges of the blank to control material flow and prevent wrinkles.
- Draw Ring: Guides the metal into the die and ensures uniform stretching.
- Pressure Pad: Maintains consistent contact between the blank and die during forming.
- Nitrogen Springs: These high-pressure gas springs replace traditional mechanical springs or hydraulic systems, providing consistent and adjustable force to the blank holder or pressure pad. They offer advantages such as compact design, reduced maintenance, and resistance to temperature fluctuations.
- Draw Punch Post: A critical support structure that aligns and stabilizes the punch during the forming process. It ensures precise vertical movement, minimizes deflection, and enhances the durability of the punch assembly.
Material selection for these components (e.g., tool steel or carbide) is critical to withstand high stresses and wear.
Material Considerations
- Sheet Metal Properties: Materials with high ductility, such as aluminum, stainless steel, or low-carbon steel, are ideal for deep drawing.
- Lubrication: Reduces friction between the die and workpiece, minimizing heat and wear. Common lubricants include oils, greases, or polymer coatings.
- Blank Preparation: Properly cut blanks with smooth edges reduce the risk of cracks during forming.
Challenges and Solutions
Deep drawing poses unique challenges:
- Wrinkling: Caused by excessive compressive stress. Solution: Increase blank holder pressure (using nitrogen springs for precise force control) or use draw beads.
- Tearing: Occurs due to over-thinning of material. Solution: Optimize punch speed, lubrication, or reduce draw depth.
- Springback: Elastic recovery of the metal after forming. Solution: Adjust die geometry, use post-forming calibration, or reinforce the draw punch post to improve punch stability.
Simulation software, such as finite element analysis (FEA), helps predict and mitigate these issues during die design.
Advanced Techniques
- Progressive Dies: Combine multiple operations (cutting, drawing, trimming) in a single die for high-volume production.
- Hydromechanical Deep Drawing: Uses fluid pressure to improve material flow and form complex geometries.
- Multi-Stage Drawing: Divides the process into steps to achieve greater depths without failure.
- Nitrogen Spring Systems: Integrated into modern dies for dynamic force adjustment, enabling better control over deep drawing of high-strength materials.
Quality Control
Critical parameters include:
- Blank Alignment: Ensures symmetry and uniform material distribution.
- Tool Maintenance: Regular inspection of dies, nitrogen springs (for pressure consistency), and draw punch posts (for alignment and wear).
- Dimensional Checks: Use coordinate measuring machines (CMMs) or laser scanning to verify part accuracy.
Future Trends
Advancements in smart dies with embedded sensors, AI-driven process optimization, and sustainable materials (e.g., recyclable alloys) are reshaping deep drawing technology. Additive manufacturing is also enabling faster prototyping of dies with intricate geometries. Innovations like self-regulating nitrogen spring systems and lightweight, high-stiffness draw punch posts (made from composite materials) are pushing the boundaries of precision and efficiency.
Conclusion
Deep drawing remains a cornerstone of modern manufacturing, enabling the mass production of lightweight, durable components. Success hinges on robust die design (including advanced components like nitrogen springs and draw punch posts), material selection, and process control. As industries demand more complex and eco-friendly products, innovation in stamping die technology—from intelligent force systems to wear-resistant tooling—will continue to drive efficiency and precision in deep drawing applications.