Tolerance in Precision Molding: Why It Matters
In the world of precision injection molding, the concept of tolerance plays a crucial role. Whether you’re manufacturing components for medical devices, automotive systems, or consumer electronics, even the slightest deviation in dimension can lead to part failure, assembly issues, or regulatory non-compliance.
In this article, we’ll explore what tolerance means in precision molding, why it matters, and how it impacts both production and end-use performance.
What Is Tolerance in Molding?
Tolerance refers to the permissible variation in a physical dimension of a molded part. In precision molding, these tolerances are extremely tight — often in the range of ±0.01 mm or less — depending on the material, geometry, and application.
For example:
- A medical syringe barrel may require a tolerance of ±0.005 mm to ensure smooth plunger movement.
- A connector housing in electronics may need tight tolerances to ensure proper mating with other components.
Why Tight Tolerances Matter
Here are key reasons why maintaining precise tolerances is critical:
- Assembly Fit
- Mismatched parts lead to poor product fit or require post-processing adjustments.
- Tight tolerances ensure seamless assembly, especially in multi-part systems.
- Functionality
- Mechanical or fluid systems (e.g., valves, pumps) depend on precision for proper function.
- Tolerances impact friction, sealing, and motion.
- Regulatory Compliance
- Industries like medical and automotive are governed by strict quality standards (ISO 13485, IATF 16949).
- Failing to meet tolerances may lead to rejection of entire batches.
- Cost Control
- Poor tolerance control increases scrap rates and quality failures.
- Achieving “just enough” precision optimizes cost-efficiency.
Factors That Affect Tolerances
- Material Shrinkage: Different resins shrink at different rates.
- Mold Design: Gate location, cooling channels, and draft angles all affect dimensional accuracy.
How GUNRI Mold Ensures Tight Tolerances
At GUNRI, we specialize in high-precision mold compontents manufacturing for global clients in the medical, automotive, and electronics sectors. Here’s how we meet tight tolerance requirements:
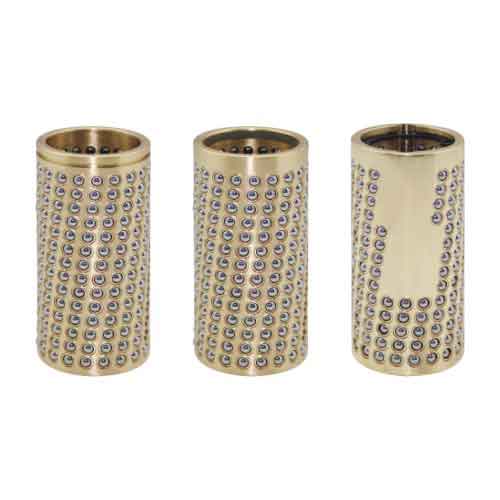
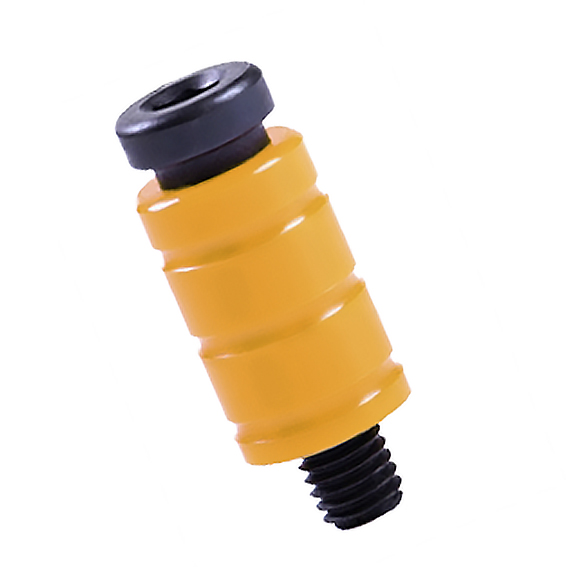
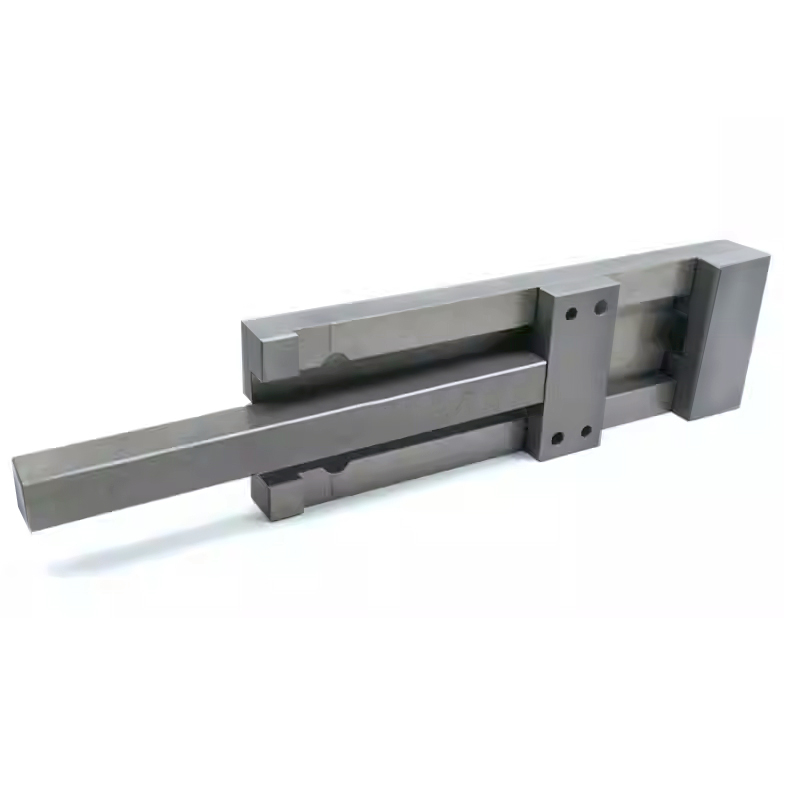
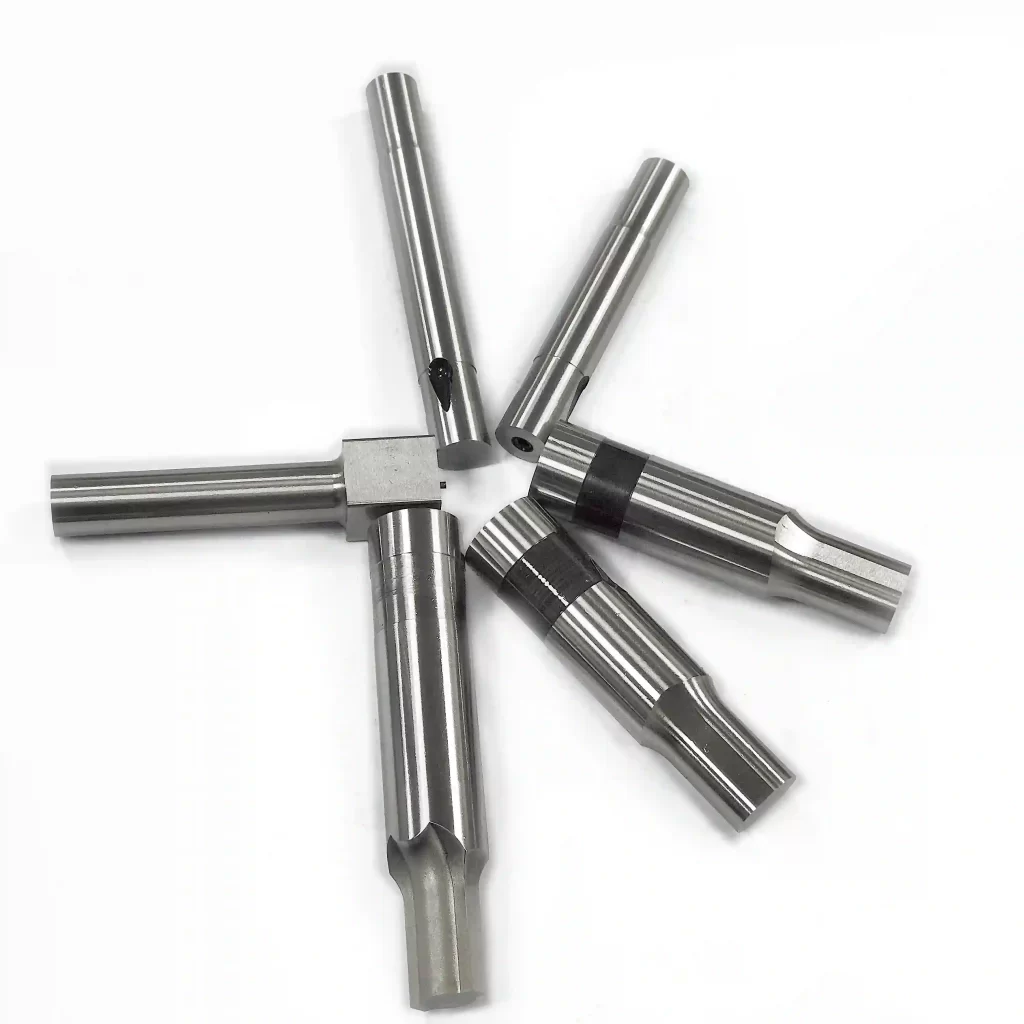
- Advanced CNC and EDM equipment with micron-level accuracy
- In-house CMM inspection to verify each part before shipment
- Extensive mold flow analysis to simulate part shrinkage and warpage
- Experience with engineering-grade resins like PEEK, LCP, and PPS
Final Thoughts
Precision molding tolerance is not just a technical detail — it’s a critical factor in your product’s performance and market success. Working with an experienced mold partner like GRMold can help you ensure that every part meets your exacting standards, from prototype to high-volume production.
Need support on your next tight-tolerance mold project? Contact us to get a free consultation and quote.