Understanding Ejector Pins in Injection Molding
Ejector pins play a crucial role in the injection molding process, ensuring the efficient and seamless production of plastic parts. These pins are indispensable in the manufacturing of high-quality components, providing precision and reliability. In this comprehensive guide, we will delve into the intricate details of ejector pins, exploring their types, functions, materials, and best practices for usage. Our goal is to provide an exhaustive resource that outshines existing content on this subject.
Table of contents
What Are Ejector Pins?
Ejector pins are slender rods used in injection molding machines to push the molded part out of the mold cavity after it has solidified. These pins are inserted into the mold base and are essential for the automatic ejection process, ensuring that the part is removed without damage. The correct selection and use of ejector pins are vital for maintaining the integrity and quality of the molded parts.
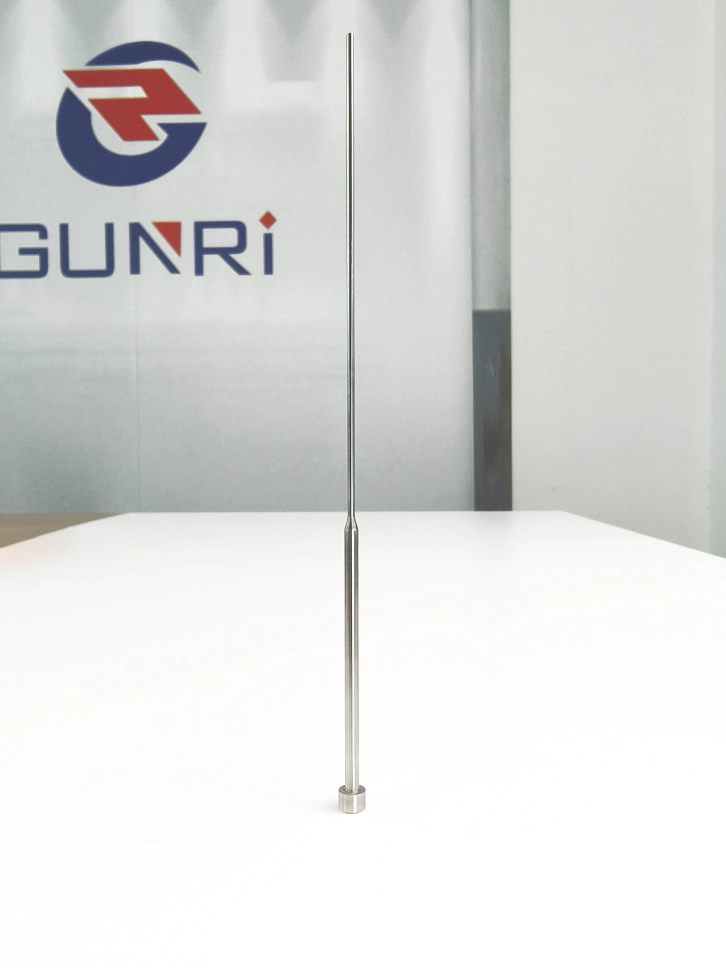
Types of Ejector Pins
There are several types of ejector pins used in injection molding, each designed for specific applications and requirements. Understanding the differences between these types can help in selecting the right pin for your project.
1. Standard Ejector Pins
Standard ejector pins are the most commonly used type. They are typically made from high-quality steel and are designed for general-purpose applications. These pins are known for their durability and ability to withstand repeated use without significant wear.
2. Blade Ejector Pins
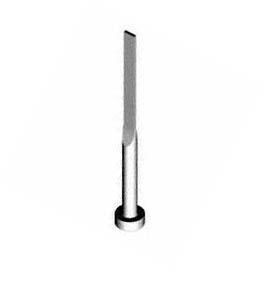
Blade ejector pins, also known as flat ejector pins, have a flat, blade-like tip. These pins are ideal for ejecting thin-walled parts or components with intricate details that standard pins might damage. Their unique design allows for more precise and delicate ejection.
3. Step Ejector Pins
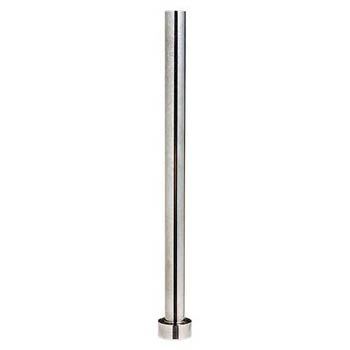
Step ejector pins feature a stepped profile, providing multiple diameters along their length. This design is useful for parts that require different levels of ejection force or for molds with complex geometries. Step ejector pins offer versatility and can be customized to fit specific needs.
4. Ejector Sleeves
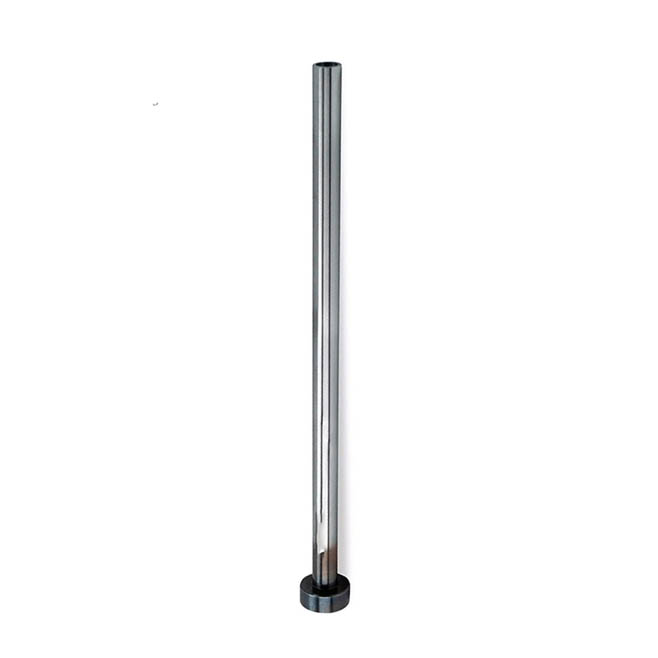
Ejector sleeves are hollow tubes that surround a core pin. They are used to eject parts with delicate or complex internal geometries, ensuring that the part is pushed out uniformly without causing damage. Ejector sleeves are particularly useful in molding applications where traditional pins might not provide adequate support.
Materials Used for Ejector Pins
The material composition of ejector pins significantly influences their performance and longevity. Selecting the appropriate material is crucial for ensuring that the pins can withstand the high temperatures and pressures involved in the injection molding process.
1. Tool Steel
Tool steel is the most common material used for ejector pins due to its excellent hardness and wear resistance. It can endure high temperatures and repeated use, making it ideal for standard applications. Tool steel pins are often coated with additional materials to enhance their properties further.
2. High-Speed Steel (HSS)
High-speed steel ejector pins are known for their superior toughness and heat resistance. HSS is suitable for applications involving higher temperatures and more abrasive materials. These pins offer a longer lifespan and reduced risk of failure under extreme conditions.
3. Stainless Steel
Stainless steel ejector pins provide excellent corrosion resistance, making them ideal for environments where moisture or corrosive materials are present. These pins are also suitable for medical and food-grade applications where hygiene is paramount.
4. Titanium
Titanium ejector pins are lightweight and possess exceptional strength and corrosion resistance. Although more expensive, they are used in specialized applications where other materials might fail, such as aerospace or medical device manufacturing.
Design Considerations for Ejector Pins
When designing ejector pins for injection molding, several factors must be taken into account to ensure optimal performance and part quality. These considerations include the pin length, diameter, tip design, and placement within the mold.
1. Pin Length and Diameter
The length and diameter of the ejector pin must be carefully calculated to provide sufficient ejection force without damaging the part. The pin should be long enough to reach the mold cavity and push the part out completely but not so long that it bends or breaks under pressure. The diameter should be appropriate for the part size and shape, ensuring uniform force distribution.
2. Tip Design
The tip design of the ejector pin is critical for preventing part damage during ejection. Common tip designs include flat, dome, and spherical tips, each suited for different part geometries. The tip should be smooth and free of burrs to avoid leaving marks on the part surface.
3. Pin Placement
Proper placement of ejector pins within the mold is essential for even ejection and part quality. Pins should be strategically positioned to avoid creating weak points or stress concentrations in the part. In some cases, multiple pins may be required to ensure balanced ejection.
Best Practices for Ejector Pin Usage
To achieve the best results in injection molding, it is essential to follow best practices for ejector pin usage. These practices help extend the lifespan of the pins and improve the quality of the molded parts.
1. Regular Maintenance
Regular maintenance of ejector pins is crucial for preventing wear and ensuring consistent performance. Pins should be inspected for signs of damage or wear and replaced as necessary. Lubrication can also help reduce friction and extend the pin’s lifespan.
2. Correct Installation
Ejector pins must be installed correctly to function properly. This includes ensuring that they are aligned with the mold cavity and that they move smoothly within their guides. Improper installation can lead to pin breakage or part damage.
3. Material Compatibility
Selecting ejector pins made from materials compatible with the molded part material is vital for preventing chemical reactions or excessive wear. For example, stainless steel pins should be used for corrosive environments, while tool steel pins are suitable for general applications.
4. Customization
In some cases, standard ejector pins may not meet the specific requirements of a molding project. Customizing the pin design, material, or coating can provide better results and improve part quality. Working with a knowledgeable supplier can help identify the best solutions for unique applications.
Common Issues and Troubleshooting
Despite careful selection and maintenance, issues with ejector pins can still arise. Understanding common problems and their solutions can help mitigate these issues and ensure smooth operation.
1. Pin Breakage
Ejector pin breakage is a common issue that can occur due to excessive force, improper installation, or material fatigue. Ensuring that the pins are properly aligned and selecting the right material for the application can help prevent breakage.
2. Part Sticking
Parts sticking to the mold can result from insufficient ejection force or incorrect pin placement. Increasing the number of pins or adjusting their placement can help achieve more even ejection. Additionally, using ejector sleeves can provide more uniform force distribution.
3. Surface Marks
Surface marks on the molded part can occur if the pin tips are not smooth or if they apply uneven pressure. Ensuring that the pin tips are free of burrs and selecting the appropriate tip design for the part geometry can help prevent surface defects.
Conclusion
In the injection molding process, ejector pins are essential components that ensure the efficient and high-quality production of plastic parts. By understanding the different types of ejector pins, their materials, and best practices for their use, manufacturers can achieve superior results and minimize issues. Proper design, maintenance, and troubleshooting are key to maximizing the performance and lifespan of ejector pins, ultimately leading to better part quality and increased productivity.
If you are interested in enhancing your injection molding process or require customized ejector pin solutions to meet your specific production needs, GUNRI is the ideal choice for you. We have a professional team and advanced technology to provide you with high-quality ejector pin products and customized services. Contact us now to learn more about our products and services, and let us help you improve production efficiency and product quality.