Understanding Ejector Pins in Injection Molding: A Comprehensive Guide
In the intricate world of injection molding, ejector pins play a pivotal role in ensuring the success of the manufacturing process. These components, though small, are essential for the efficient and precise production of plastic parts. This article delves into the intricacies of ejector pins in injection molding, exploring their types, functions, materials, and best practices for their usage.
What Are Ejector Pins?
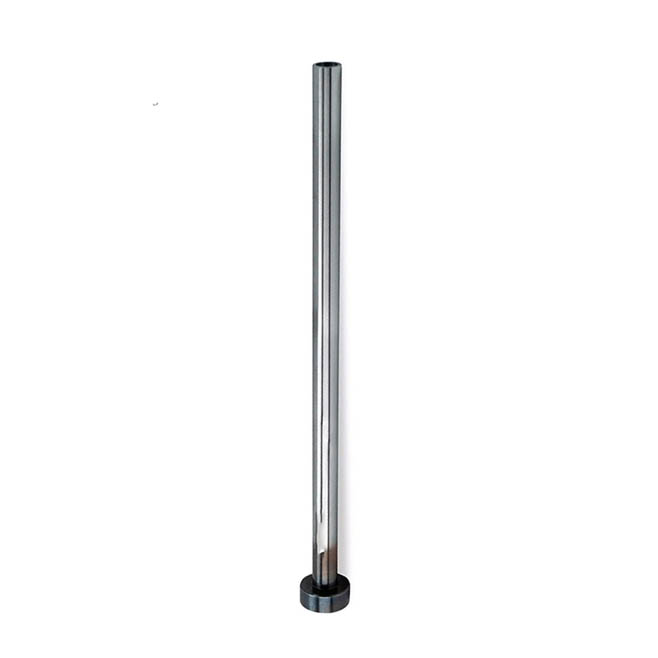
Ejector pins are slender rods that are employed in injection molding machines to eject the molded part from the mold after it has solidified. The role of these pins is crucial because, without them, the molded part would remain stuck in the mold, potentially causing defects or damage to the part or the mold itself. Ejector pins are designed to penetrate the mold cavity and push the part out, ensuring a clean and precise release.
Types of Ejector Pins
There are several types of ejector pins used in injection molding, each designed for specific applications and materials. Understanding the different types is essential for selecting the right pin for a particular project.
1. Standard Ejector Pins
Standard ejector pins are the most commonly used type in injection molding. These pins are typically cylindrical and made of high-quality steel, which provides durability and resistance to wear. They are designed to push the molded part out of the cavity with minimal impact on the part’s surface.
2. Step Ejector Pins
Step ejector pins feature a stepped design that allows for precise ejection in cases where the molded part has complex geometries. The step design ensures that different sections of the part are pushed out at different times, reducing the risk of part deformation or damage.
3. Blade Ejector Pins
Blade ejector pins are thin, flat pins used for ejecting parts with narrow or delicate sections. These pins are particularly useful for parts that have intricate designs or thin walls, where standard pins might cause damage or leave marks.
4. Ejector Sleeves
Ejector sleeves are a type of ejector pin that surrounds the core pin. They are used in applications where the part has a central hole or requires uniform ejection around a core. Ejector sleeves provide even pressure during ejection, ensuring that the part is removed smoothly and without distortion.
Materials Used for Ejector Pins
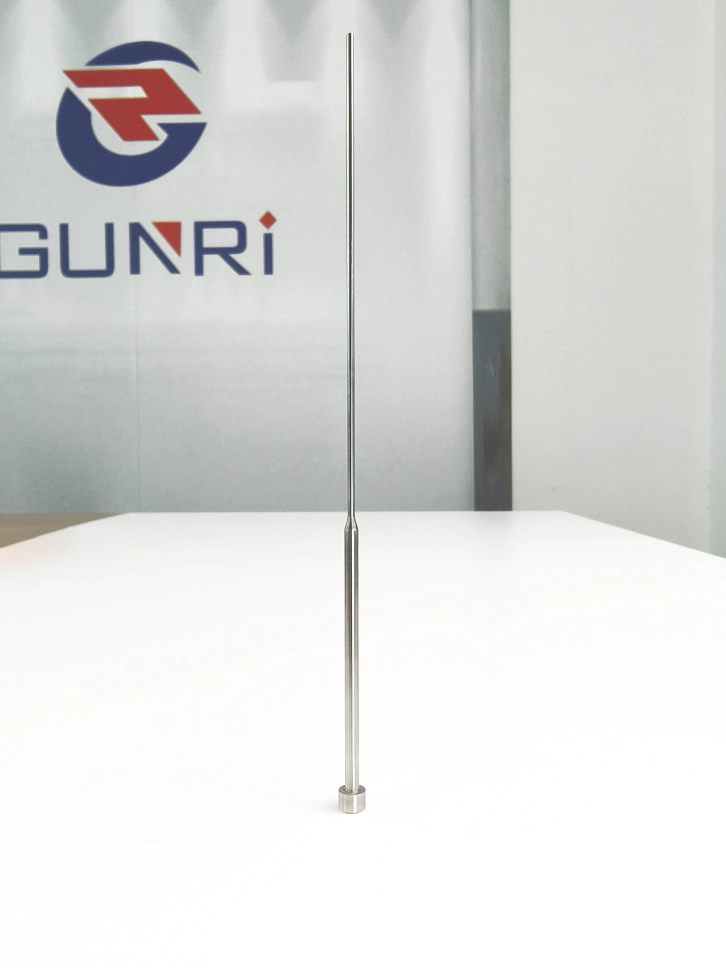
The material used for ejector pins is critical to their performance and longevity. The choice of material depends on factors such as the type of plastic being molded, the operating temperature, and the required durability.
1. Tool Steel
Tool steel is the most commonly used material for ejector pins due to its excellent hardness, wear resistance, and toughness. It is well-suited for high-volume production and can withstand the repeated stresses of the injection molding process.
2. Stainless Steel
Stainless steel is used for ejector pins when corrosion resistance is a priority. This material is ideal for molding applications where the pins are exposed to moisture or corrosive substances. Stainless steel pins also offer good wear resistance and durability.
3. H13 Steel
H13 steel is a high-performance alloy that is often used for ejector pins in demanding applications. It offers excellent toughness, heat resistance, and wear resistance, making it suitable for high-temperature molding processes.
4. Titanium
Titanium ejector pins are used in specialized applications where lightweight and corrosion resistance are essential. Although more expensive than other materials, titanium offers superior performance in specific environments.
The Role of Ejector Pins in the Injection Molding Process
Ejector pins are integrated into the injection molding process during the design phase of the mold. Their placement and movement must be carefully planned to ensure that the molded part is ejected without defects. The following sections outline the key considerations in using ejector pins effectively.
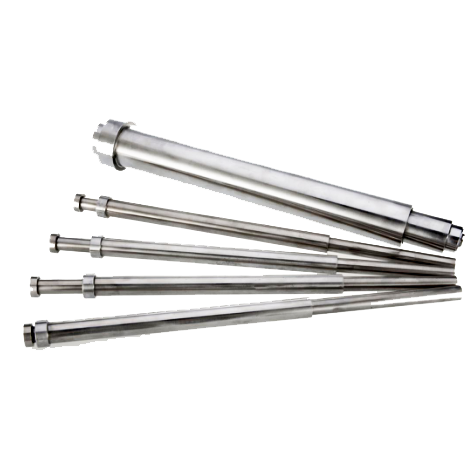
1. Pin Placement
The placement of ejector pins is critical to avoid visible marks on the finished part. Pins are usually positioned in areas that are less visible or that will be machined or assembled later. Strategic placement ensures that the ejection process does not compromise the part’s aesthetic or functional qualities.
2. Ejection Force
The force required to eject the part from the mold must be carefully calculated. Too much force can cause the part to deform, while too little force may result in incomplete ejection. The material of the part, its design, and the type of ejector pin all influence the ejection force.
3. Timing of Ejection
The timing of ejection is another critical factor. The part must be fully cooled and solidified before ejection to avoid warping or other defects. Proper cooling times and controlled ejection speeds are essential to achieving a flawless part.
4. Maintenance and Wear
Regular maintenance of ejector pins is necessary to ensure their continued performance. Pins can wear over time due to friction and repeated use, leading to increased risks of part defects. Routine inspection and replacement of worn pins are crucial for maintaining the quality of the molding process.
Common Challenges and Solutions
Despite their importance, ejector pins can present challenges in the injection molding process. Below are some common issues and their solutions.
1. Pin Marks on Parts
Pin marks can occur when the ejector pins leave impressions on the part’s surface. This issue can be minimized by optimizing pin placement, using smaller pins, or incorporating pin sleeves to distribute the ejection force more evenly.
2. Sticking of Parts in the Mold
Parts that stick to the mold can cause delays and defects. This problem is often due to improper cooling or insufficient ejection force. Adjusting the cooling time and increasing the ejection force can help resolve this issue.
3. Pin Breakage
Ejector pins can break due to excessive force, improper alignment, or material fatigue. Using pins made from high-quality materials, ensuring proper alignment, and regularly inspecting the pins for wear can reduce the risk of breakage.
Best Practices for Ejector Pin Selection and Use
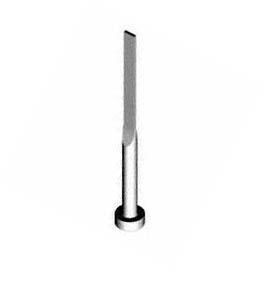
To maximize the efficiency and quality of the injection molding process, it is essential to follow best practices when selecting and using ejector pins.
1. Material Selection
Choose the right material for the ejector pins based on the specific requirements of the molding process. Consider factors such as the type of plastic, mold temperature, and the expected production volume.
2. Precision Manufacturing
Ensure that ejector pins are manufactured to precise tolerances. Even slight deviations in pin diameter or length can affect the ejection process and the quality of the finished part.
3. Regular Maintenance
Implement a regular maintenance schedule for the ejector pins. This includes cleaning, inspecting for wear, and replacing any damaged pins. Proper maintenance helps prevent defects and extends the life of the pins.
4. Collaboration with Mold Designers
Work closely with mold designers to optimize the placement and operation of ejector pins. Early collaboration can prevent issues related to pin placement and ensure that the mold design supports efficient ejection.
Conclusion: Partner with GUNRI for Precision Ejector Pins
Ejector pins may be small, but they are a vital component of the injection molding process. Their proper selection, placement, and maintenance are key to producing high-quality molded parts efficiently. By understanding the types, materials, and best practices associated with ejector pins, manufacturers can enhance the performance of their injection molding operations and achieve superior results.
At GUNRI, we specialize in providing high-precision ejector pins tailored to meet the specific needs of your injection molding projects. Our commitment to quality, combined with our extensive industry experience, ensures that you receive the best products to optimize your manufacturing process. If you’re looking to elevate your production capabilities with top-tier ejector pins, contact GUNRI today and discover how we can support your business with reliable and efficient solutions.
{stop article}