Understanding Essential Components in Injection Molding: Ejector Pins, Ejector Blades, Ejector Sleeves, and Core Pins
Injection molding is a highly versatile and widely used manufacturing process, allowing for the production of a wide range of plastic and metal parts. Key to the success of injection molding are several essential components, including ejector pins, ejector blades, ejector sleeves, and core pins. In this article, we will delve into the roles and significance of these crucial elements in the injection molding process.
Table of contents
1. Ejector Pins
Ejector pins are indispensable in injection molding as they play a vital role in the ejection of the molded part from the mold cavity. These small cylindrical pins are strategically placed within the mold and are designed to exert force on the finished part, pushing it out of the mold as it opens. Ejector pins must be precisely positioned and engineered to ensure smooth ejection without damaging the part.
2. Ejector Blades
Ejector blades, also known as ejector blades or ejector stripper plates, complement the function of ejector pins. These flat, blade-like components are located on the ejector side of the mold and are responsible for providing additional support during the ejection process. They help ensure the molded part separates cleanly from the core and cavity, preventing any potential sticking or distortion.
3. Ejector Sleeves
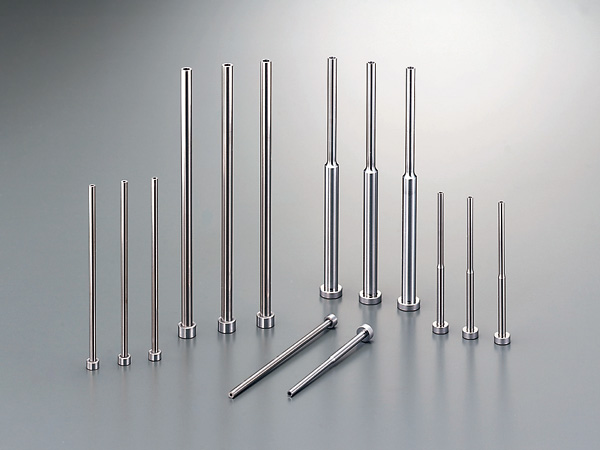
Ejector sleeves, sometimes referred to as ejector sleeves or guide pins, serve as a guiding mechanism for ejector pins and blades. These cylindrical components are precisely machined and fit snugly around the ejector pins. Ejector sleeves help maintain alignment and stability during the ejection phase, enhancing the overall efficiency of the molding process.
4. Core Pins
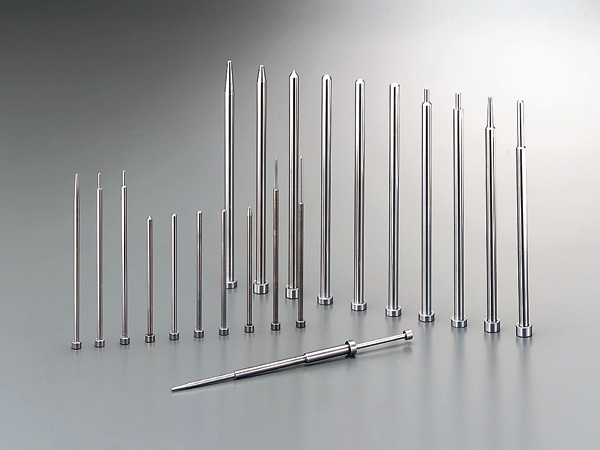
Core pins are integral components that shape the interior features of the molded part. They are designed to create cavities and voids within the part, contributing to its final form and functionality. Core pins are positioned within the mold to form intricate shapes, holes, and undercuts in the finished product. Precision in the design and manufacturing of core pins is essential for achieving accurate and consistent results.
In summary, the successful execution of injection molding relies heavily on the careful integration and precise functioning of ejector pins, ejector blades, ejector sleeves, and core pins. These components work in harmony to facilitate the efficient ejection of molded parts while ensuring the creation of complex and precise interior features. Their accurate design and meticulous manufacturing are essential for achieving high-quality, repeatable results in the injection molding process.
Production process of ejector pins
The production process of ejector pins involves several key steps:
Material Selection
The first step in producing ejector pins is selecting the appropriate material. Ejector pins are typically made from high-quality tool steels, such as H13, D2, or A2, due to their excellent wear resistance and durability. The choice of material depends on factors like the type of material being molded, the expected production volume, and the desired longevity of the ejector pins.
Cutting and Machining
Once the material is selected, it undergoes cutting and machining processes. Initially, the steel is cut into blanks of the desired length. Then, precision machining techniques, including turning, milling, and grinding, are employed to shape the ejector pins to their final dimensions. This phase demands extreme precision to ensure that the pins meet the exact specifications required for the injection molding application.
Heat Treatment
Ejector pins must exhibit excellent hardness and toughness to withstand the rigors of injection molding. Heat treatment, such as quenching and tempering, is employed to achieve the desired hardness and mechanical properties. This process enhances the pins’ wear resistance and durability, ensuring they can endure the repeated stresses of the ejection process without deformation.
Surface Finish
The surface finish of ejector pins is critical to their performance. Polishing and surface treatment processes, such as nitriding or coating with materials like titanium nitride (TiN), are often employed to reduce friction and wear, making the pins more efficient in their ejection function.
Quality Control
Throughout the production process, strict quality control measures are in place to ensure the precision and reliability of the ejector pins. Measurements, inspections, and testing are conducted to verify that the pins meet the specified tolerances and quality standards.
Packaging and Delivery
Once the ejector pins have passed quality control checks and meet the required specifications, they are carefully packaged to protect them during transportation and storage. They are then delivered to manufacturers and mold makers for integration into injection molds.
It’s important to note that the production of ejector pins demands a high level of precision and attention to detail to ensure the reliable and consistent ejection of molded parts. The quality of the ejector pins directly impacts the efficiency and performance of the injection molding process, making them a crucial component in the manufacturing industry.