1. What Are Ball Cages?
Ball cages, also referred to as ball retainers, ball cage bush or ball guides, are mechanical components used in precision engineering and motion systems. These compact structures play a crucial role in bearings and linear motion assemblies by containing and guiding a set of balls within a defined space. The primary purpose of ball cages is to maintain uniform spacing and alignment of the balls, ensuring smooth and consistent movement while minimizing friction.
Ball cages are meticulously designed to distribute the load evenly across the balls, preventing contact and reducing wear. This results in improved efficiency, reduced heat generation, and enhanced bearing life. These cages are commonly manufactured from materials such as steel, brass, or advanced polymers, chosen based on factors like load-bearing capacity, durability, and corrosion resistance.
In various industries ranging from automotive to aerospace, ball cages find applications in intricate machinery, robotics, medical devices, and more. They contribute to accurate linear motion, precise positioning, and reduced vibration. The design of ball cages varies, from simple configurations for standard bearings to complex arrangements that accommodate angular misalignment or high-speed applications.
In summary, ball cages are essential components that optimize the performance of bearings and linear motion systems. By maintaining ball alignment and distributing loads effectively, they play a pivotal role in achieving smooth and efficient movement across diverse industries and applications.
2. What Are the Applications of Ball Cages?
Ball cages find a wide range of applications across various industries due to their ability to provide controlled motion, reduced friction, and enhanced durability. Some key applications of ball cages include:
-
Automotive Systems: Ball cages are crucial components in automotive steering systems, transmissions, and suspension systems. They enable smooth and precise movement, contributing to vehicle performance and safety.
-
Industrial Machinery: In industrial equipment such as conveyors, robotics, and manufacturing machinery, ball cages facilitate linear motion and support heavy loads, ensuring efficient and reliable operations.
-
Aerospace and Aviation: Ball cages are used in aerospace applications to ensure precise movement in control systems, actuators, and landing gear mechanisms, where accuracy and reliability are paramount.
-
Medical Devices: Ball cages play a role in medical equipment such as surgical robots, diagnostic machines, and precision instruments, enabling smooth and controlled motion for accurate procedures.
-
Electronic Manufacturing: In electronics production equipment, ball cages aid in guiding components during assembly processes, contributing to the precision and quality of electronic devices.
-
Renewable Energy: Ball cages are utilized in wind turbine pitch and yaw systems, solar tracking mechanisms, and hydroelectric power generation, enabling efficient energy conversion.
-
Packaging Machinery: Ball cages ensure the smooth movement of packaging equipment components, improving the speed and accuracy of packaging processes.
-
Printing and Paper Handling: In printing presses and paper handling machines, ball cages enable precise motion in paper feed mechanisms and print head positioning.
-
Textile Industry: Ball cages are employed in textile machinery for guiding threads and fabrics, enhancing the efficiency and precision of weaving and knitting processes.
-
Machine Tools: Ball cages play a vital role in machine tools, guiding cutting tools and workpieces with accuracy, leading to high-quality machining operations.
-
Construction Equipment: Ball cages are used in construction machinery, providing smooth motion and load distribution in equipment such as cranes and excavators.
The diverse applications of ball cages across industries underscore their importance in facilitating smooth, accurate, and efficient motion, contributing to the functionality and reliability of various mechanical systems and equipment.
3. What Is the Difference between Ball Cages for Die and for Guide?
The primary difference between ball cages and plastic cages lies in their material composition. Ball cages are typically made from metals like steel or brass, whereas plastic cages are constructed using synthetic polymers. This distinction impacts properties such as durability, load-bearing capacity, and friction. Metal ball cages offer greater strength and heat resistance, making them suitable for high-load applications.
On the other hand, plastic cages excel in corrosion resistance and are often used in environments where metal cages may deteriorate. The choice between the two depends on factors like application requirements, operating conditions, and cost considerations.
4. What Is the Difference between Bi-Metal and Ball Cages?
Ball cages for dies are designed to facilitate movement within molds and dies, ensuring smooth operation and efficient ejection of finished products. On the other hand, ball cages for guides are utilized in linear motion systems, providing precise guidance and reducing friction in machinery and equipment. While both serve to enhance motion, their specific applications and design considerations differ.
Ball Cages for Dies: Ball cages used in dies are crucial for applications such as injection molding. They enable the smooth movement of ejector pins and other components, ensuring efficient release of molded parts from the mold cavities. These cages are designed to withstand high pressures and forces exerted during the molding process, while maintaining accurate ball alignment for consistent operation.
Ball Cages for Guides: Ball cages used in linear motion guides provide controlled motion along linear pathways, minimizing friction and ensuring accurate positioning. They are commonly used in machinery such as CNC routers, robotics, and industrial automation systems. These cages reduce wear and tear on moving parts, contributing to the longevity and precision of the equipment.
In summary, ball cages for dies facilitate the ejection of molded parts from molds, while ball cages for guides ensure smooth and precise linear motion in various machinery and equipment applications. The specific design and material choices for each type of ball cage are tailored to their distinct roles in enhancing operational efficiency and accuracy.
5. Is Ball Cage Self-Lubricating?
Ball cages themselves are not inherently self-lubricating. However, lubrication can be applied to the balls within the cage to minimize friction and enhance the overall efficiency of the bearing or motion assembly.
6. What Are Cast and Self-Lubricating Ball Cages?
Cast ball cages are manufactured through casting processes, resulting in intricate designs that facilitate ball movement. Self-lubricating ball cages integrate lubrication channels or pockets within the cage structure, allowing for continuous lubrication distribution over time.
7. Do Ball Cages Need Greasing?
While ball cages do not require direct greasing, it’s common practice to apply lubrication to the balls to reduce friction and wear. Self-lubricating designs minimize the need for frequent greasing, making them suitable for applications with limited maintenance access.
8. What Material Can Be Used for Ball Cages If Copper, Zinc, and Nickel are Prohibited?
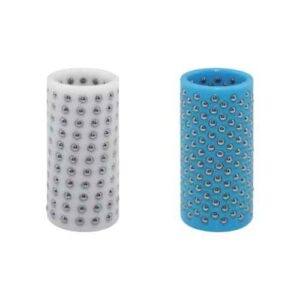
If there are restrictions on using copper, zinc, and nickel materials for ball cages, an excellent alternative is Polyoxymethylene (POM), commonly referred to as acetal or Delrin. POM is a versatile engineering plastic renowned for its exceptional mechanical properties, including high wear resistance, low friction coefficient, and excellent dimensional stability.
Polyoxymethylene possesses a unique set of attributes that make it suitable for applications where copper, zinc, and nickel are prohibited due to specific requirements or environmental considerations. Notably, POM is inherently non-metallic, thus addressing concerns related to prohibited metals.
One of POM’s key advantages is its self-lubricating property, which contributes to reduced friction and wear in ball cage applications. This feature not only enhances the efficiency and longevity of the components but also eliminates the need for external lubrication.
Furthermore, POM exhibits excellent resistance to various chemicals and solvents, making it well-suited for diverse industrial settings. Its dimensional stability ensures consistent performance even in challenging conditions, and its relatively low moisture absorption helps maintain its properties over time.
The non-metallic nature of POM is particularly beneficial in applications where metal contamination must be minimized, such as those involving sensitive electronic or medical equipment. Additionally, POM’s lightweight nature is advantageous in applications where weight reduction is a consideration.
When faced with restrictions on copper, zinc, and nickel materials, POM emerges as a reliable solution, offering a combination of mechanical strength, self-lubrication, corrosion resistance, and non-metallic characteristics. Manufacturers seeking compliance with specific material requirements can confidently explore POM as an alternative material choice for their ball cage applications.
9. What Material Can Be Used for Ball Cages to Prevent Rust?
If a ball cage requires rust prevention, the material choice that stands out is SUS440C stainless steel. SUS440C is renowned for its exceptional corrosion resistance properties, making it an ideal option for environments where rust is a concern. This stainless steel grade performs admirably even in conditions that are damp or humid. By opting for SUS440C, you can ensure prolonged durability and reliable performance of the ball cage, especially in settings prone to rust-related challenges.
The high resistance to corrosion that SUS440C offers stems from its composition, which includes chromium and molybdenum. These elements create a protective layer on the surface, shielding the material from oxidizing agents that lead to rust formation. As a result, ball cages made from SUS440C stainless steel can maintain their structural integrity and functionality over extended periods, even when exposed to potentially corrosive elements.
10. Who Is the Best Ball Cage Manufacturer in China?
When discussing the top ball cage manufacturers in China, Gunri stands out as a premier choice.
Gunri is a highly regarded brand with certifications including ISO 9001-2015 and other relevant business credentials.
Having earned the trust of a vast clientele worldwide, both domestic and international customers vouch for Gunri’s exceptional products and services.
For all your requirements, you can confidently turn to Gunri. The company’s expertise extends to assisting you in finding the most suitable manufacturer in your vicinity as well.
Furthermore, Gunri boasts an impressive production capacity for ball cages. The ability to manufacture thousands of units daily ensures a consistent supply even during peak demand periods.
Employing advanced automation in our manufacturing processes guarantees a steady flow of ball cages at all times.
As an added advantage, we offer complimentary samples of our ball cages, enabling you to assess their quality before proceeding with your order.
To provide you with comprehensive insight, detailed images and videos of each product are also available.
Just as in the case of the best ball cage manufacturer in China, our company, Gunri, maintains a commitment to excellence, reliability, and customer satisfaction.
The production process of ball cage:
11. Can I Get Customized Ball Cages?
Certainly, you have the option to obtain customized bronze bearings tailored to your specific requirements.
Gunri is equipped to swiftly produce a diverse range of self-lubricated bearings.
Our products are characterized by advanced technology and exceptional materials in their construction.
Having earned a longstanding reputation, Gunri has consistently proven to be a top-tier manufacturer of bronze bushings. As dedicated professionals, we guarantee the supply of superior materials.
To procure your personalized bronze bushings, simply provide us with the design, specifications, material preferences, and dimensions. Within a week, you’ll receive a customized order tailored precisely to your needs.
Just as with the customized ball cages, we extend the same dedication to catering to your unique specifications and ensuring the highest quality. Your satisfaction is our utmost priority.
12. What Is the Load Carrying Capacity of Ball Cages?
The load carrying capacity of ball cages varies based on factors such as the design, materials used, ball size, and the specific application they are intended for. Generally, ball cages are engineered to withstand both radial and axial loads, making them suitable for a wide range of industrial and mechanical applications.
In applications with linear motion, such as CNC machines and robotics, ball cages are designed to distribute loads evenly across multiple balls, minimizing wear and ensuring smooth movement. The load capacity of a ball cage is influenced by the number of balls it contains, their size, and the contact angle between the balls and the raceways.
For higher load-carrying capacity, ball cages often utilize larger ball diameters, which can distribute heavier loads while maintaining stability. Additionally, material choice is critical. Stainless steel and hardened steel are common materials for ball cages, offering excellent strength and durability.
It’s essential to refer to manufacturer specifications and consult with experts to determine the load capacity of ball cages for your specific application. Factors such as load direction, speed, and operating conditions play a significant role in determining the optimal ball cage design for reliable and efficient load distribution.
15. What Are the Advantages of Using Ball Cages?
Using ball cages offers several distinct advantages across various industries and applications. These advantages stem from their ability to enhance precision, reduce friction, and improve overall mechanical performance. Here are some key benefits of using ball cages:
-
Reduced Friction: Ball cages significantly reduce friction between moving parts, ensuring smoother and more efficient motion. This reduction in friction leads to lower wear and tear on components, contributing to increased longevity and reduced maintenance needs.
-
Precise Linear Motion: In linear motion systems, ball cages provide precise guidance for smooth and accurate movement. This accuracy is crucial in applications where positioning and alignment are critical, such as CNC machines, robotics, and automation equipment.
-
Load Distribution: Ball cages distribute loads evenly across multiple balls, preventing concentrated stress on individual components. This even distribution enhances load-carrying capacity and minimizes the risk of premature component failure.
-
Minimized Play and Backlash: Ball cages help eliminate play and backlash in mechanical systems, ensuring minimal movement between parts and enhancing positional accuracy. This is crucial in applications where precision and consistency are paramount.
-
Improved Efficiency: By reducing friction and ensuring smooth motion, ball cages contribute to increased efficiency in various systems, from manufacturing equipment to automotive mechanisms. This efficiency translates to reduced energy consumption and optimized performance.
-
Noise Reduction: The controlled movement offered by ball cages can help dampen vibrations and reduce noise levels, making them ideal for applications where quiet operation is essential, such as medical devices and consumer electronics.
-
High-Speed Capability: Ball cages allow for smooth and controlled motion at high speeds without sacrificing accuracy. This makes them suitable for applications requiring rapid movement, like conveyor systems and high-speed machinery.
-
Versatility: Ball cages are versatile components that find application in a wide range of industries, from aerospace and automotive to electronics and manufacturing. Their adaptability stems from their ability to improve motion and reduce wear in diverse systems.
-
Maintenance Reduction: Due to their durability and reduced wear characteristics, systems incorporating ball cages experience less frequent maintenance requirements. This results in decreased downtime and increased operational efficiency.
-
Enhanced Product Quality: The precision and accuracy facilitated by ball cages contribute to improved product quality across various manufacturing processes. This ensures consistent outcomes and reduces defects.
In summary, the advantages of using ball cages encompass improved precision, reduced friction, enhanced load distribution, and increased efficiency. These benefits make ball cages indispensable components in various applications where controlled motion, accuracy, and reliability are crucial.