China guide pillar and guide bush manufacturer
Whether you need high-precision positioning or long-lasting durability,
our guide pillars and guide bushes can meet your requirements.
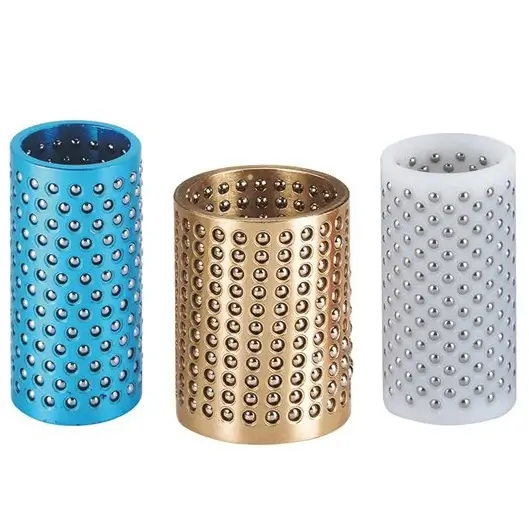
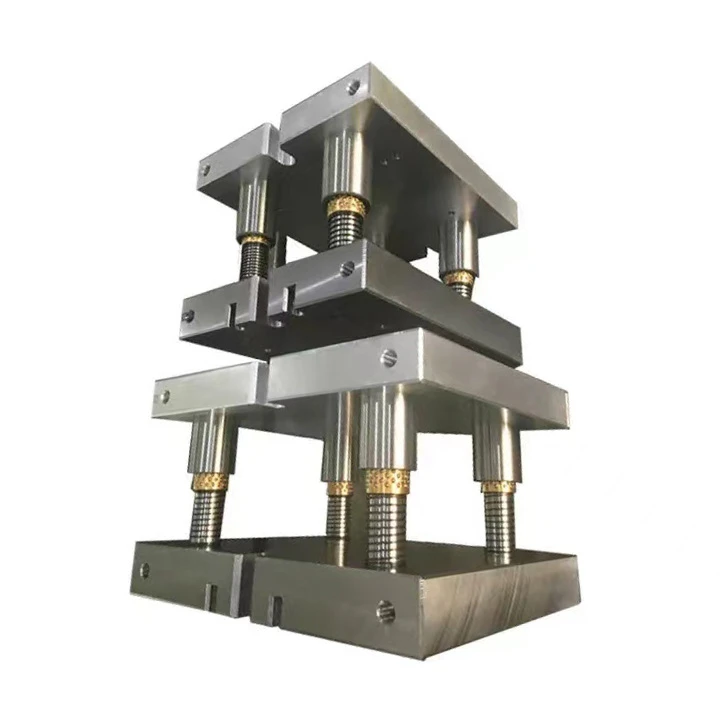


Whether you need high-precision positioning or long-lasting durability,
our guide pillars and guide bushes can meet your requirements.
Guide Pillars used in different mold projects vary,Here are some popular product videos.
If you require additional information, please feel free to contact us at your earliest convenience.
Gunri, established in 2006, specializes in the manufacturing of molds and mold components, including punch pins, ball cages, ejector pins, dowel pins, guide pillars, guide bushes, CNC parts, and more.
Our products are exported worldwide, and our primary focus is on sustainable growth, delivering high-quality products, and reducing costs for our global clients.
Gunri also provides OEM contract manufacturing services for renowned brands like MISUMI, FIBRO, HASCO, and others to meet their custom requirements.
Welcome to contact us, whether you are looking for mold components, have questions, want to provide suggestions, or seek collaboration opportunities.
We specialize in providing high-quality components for the mold manufacturing industry, and our team is ready to provide support and answer your questions at any time.
Guide pillars are essential components in molds, ensuring precise positioning and guiding the movement of the mold during operation. They are commonly paired with components to facilitate accurate alignment and guide the mold’s travel.
The most prevalent guiding mechanism is the use of guide pillars and bushings. In addition, larger molds may incorporate guide plates, while smaller punch dies might utilize guide pins.
In the context of standard components in automotive molds, guide bushings are often employed for drilling and boring purposes. The ones used for drilling are referred to as drill bushings, and those for boring are called tool rod guide bushings. Their role is to secure the drill or tool rod, preventing deviation during cutting. This helps enhance the dimensional and positional accuracy of the machined holes.
By Direction:
By Installation Method:
By Application:
Characteristics of Guide Pillars:
The main reasons for the easy wear and tear of guide pillars and bushings are as follows:
Poor Quality: The choice of inferior materials and inadequate hardness during the production of guide pillars and bushings results in lower product quality, making them prone to damage and scratches.
Poor Fit: Insufficient fit between guide pillars and bushings makes them susceptible to pulling and wear, leading to damage.
Unreasonable Design: Poorly designed guide pillars and bushings can create significant suction during vacuum molding after the molds are closed, increasing the risk of damage.
Lack of Timely Cleaning and Maintenance: Regular cleaning of mold surfaces and the application of lubricating oil should be performed during each shift to ensure proper maintenance and extend the lifespan.
In mold design, inclined guide pillars commonly have angles of either 20 degrees or 25 degrees. The most frequently used angle is 20 degrees. If the slide distance is somewhat long, a 25-degree angle may be employed. For even longer distances, hydraulic or pneumatic methods should be considered.
The roundness of guide pillars has strict requirements. Drilling a center hole is primarily done to facilitate the use of external cylindrical grinders for grinding the outer diameter.
During the grinding process with an external cylindrical grinder, the guide pillar needs to be rotated by being supported at the center hole using a center point.
Lubrication Performance: Guide pillars should exhibit excellent lubrication performance, and lubrication oil grooves may be incorporated when necessary.
Structural Strength: The fixed portion diameter of the guide pillar should be 1.5 to 2 times the diameter of the working portion to ensure adequate structural strength.
Surface Roughness: The roughness (Ra) of the working surface of the guide pillar should not exceed 0.63μm to maintain precision in sliding coordination.
Hardness: The guide pillar surface should be wear-resistant and have a hardness of 50~55HRC after heat treatment.
Geometric Design: The front end of the guide pillar should feature a conical angle of 3-5 degrees or be designed in a conical shape to enhance precision in coordinating positions with two templates.
Length: The length of the guiding portion of the guide bushing should exceed the height of the core end face by 8~12mm.
Shape: The interior of the guide bushing should allow smooth entry of the guide pillar; thus, the front end of the guide pillar can be designed as a conical frustum or a hemisphere.
Material: The guide bushing should be made of a hard and wear-resistant material to ensure both guiding performance and durability.
Surface Roughness: The surface roughness of the guide bushing should be moderate to ensure smooth guidance.
Material Matching: Guide pillars are typically made of bearing steel, hot work tool steel, etc., ensuring good guiding performance and durability.
Arrangement: Guide pillars should be evenly distributed around the mold parting surface, with a sufficient distance from the center to the mold edge to ensure mold strength.
Directionality: To ensure unidirectional mold closure, the arrangement of guide pillars can employ asymmetrical placement of equal-diameter guide pillars or symmetrical placement of unequal-diameter guide pillars.
Material Used: SUJ2
Hardness: HRC58 or above. The dimensions and positional accuracy of guide pillars and bushings are strictly controlled within 0.003mm (Gunri can control within 0.002mm); especially for high rigidity guide pillar components, the arrangement density of steel balls in the steel ball retainer is 1.7 times that of a regular steel ball retainer, increasing the point contact of guide pillars and bushings through steel balls by 70%.