In the realm of modern manufacturing, efficiency and precision are paramount. The Ball Lock punch and die system has emerged as a groundbreaking solution, significantly streamlining tool and die changes in industries like stamping, mold manufacturing, and tooling. By eliminating the need for traditional fastening methods, this innovative mechanism empowers manufacturers to achieve rapid setups, enhanced accuracy, and increased productivity.
Understanding Ball Lock Technology
The Ball Lock punch and die system operates on a simple yet ingenious principle. It comprises several key components:
- Shank: The foundation of the system, providing a robust connection to the tool plate.
- Balls: The core locking mechanism, ensuring a secure and precise fit.
- Locking Sleeve: Controls the engagement and disengagement of the balls, enabling quick tool changes.
To activate the system, the locking sleeve is manipulated to move the balls into or out of a predefined position. This action either locks the tool or die in place or releases it, ensuring a secure and repeatable connection.
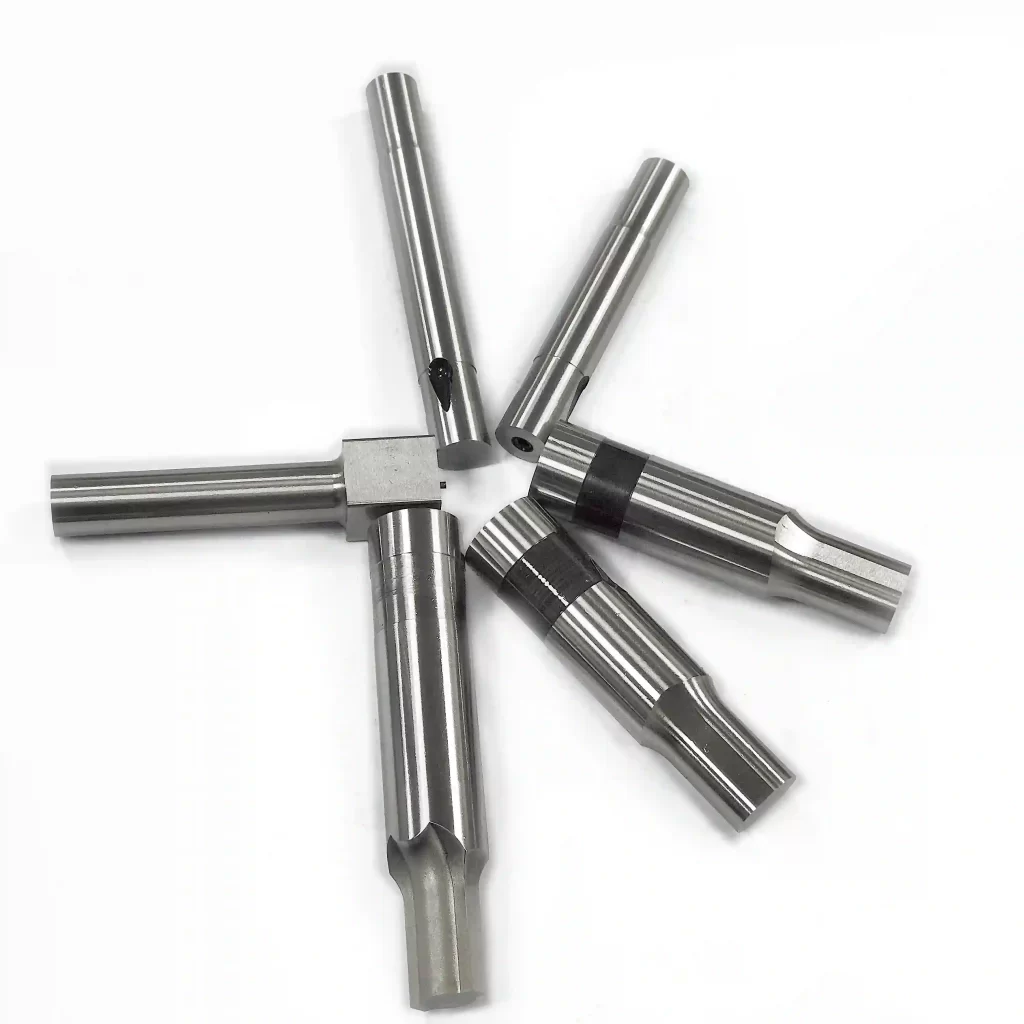
Key Advantages of Ball Lock Punch and Die
- Rapid Tool Changes: The Ball Lock system significantly reduces downtime by eliminating the need for time-consuming screw fastening methods. Tool changes can be accomplished in mere seconds, maximizing production efficiency.
- Enhanced Precision: The precise alignment and locking mechanism ensure consistent and accurate tool positioning, resulting in improved product quality and reduced scrap rates.
- Increased Productivity: Faster tool changes translate to increased production output, leading to higher overall efficiency.
- Reduced Costs: Lower downtime and increased productivity directly contribute to cost savings.
- Enhanced Safety: The simplified tool change process minimizes the risk of accidents and injuries.
- Versatility: Compatible with a wide range of tools and dies, making it suitable for various applications.
Applications Across Industries
The Ball Lock punch and die system finds applications in numerous industries:
- Sheet Metal Stamping: Rapid die and punch changes for efficient production of automotive components, appliances, and other metal products.
- Mold Manufacturing: Secure fastening of cores and cavities in plastic and rubber mold making, ensuring precision and repeatability.
- Automotive Industry: High-precision tool changes for manufacturing critical components like engine blocks, transmission housings, and body panels.
- Aerospace Industry: Reliable and efficient tool changes for aerospace manufacturing, where precision and quality are paramount.
- Food and Pharmaceutical Industries: Hygienic and quick tool changes for sanitary production environments, ensuring product safety and compliance with regulatory standards.
Materials and Construction
Ball Lock components are typically made from high-quality materials to ensure durability and reliability:
- Shank: Alloy steel for superior strength and rigidity.
- Balls: Hardened steel or ceramic for optimal performance and longevity.
- Locking Sleeve: Precision-engineered for smooth operation and durability.
- Surface Treatments: Specialized coatings to enhance corrosion resistance, wear resistance, and overall performance.
Conclusion
The Ball Lock punch and die system has revolutionized the tooling industry, offering a reliable, efficient, and safe solution for tool and die changes. By understanding its features, working principle, advantages, and applications, manufacturers can leverage this technology to optimize their production processes, reduce downtime, and achieve significant improvements in productivity and quality.
Additional Considerations
- Ball Lock Punches and Dies: These are specific types of tools that utilize the Ball Lock system for quick and precise attachment to the press or stamping machine.
- Punch Retainer Systems: These systems, often used in conjunction with Ball Lock technology, provide additional support and stability for punches and dies.
- Heavy Duty Punches and Light Duty Punches: These terms refer to the capacity and strength of punches, with heavy-duty punches being suitable for thicker materials and more demanding applications.
By understanding these additional concepts, manufacturers can select the most appropriate Ball Lock solutions for their specific needs.